Tearable non-woven fabric making method
A production method and non-woven technology, which can be used in non-woven fabrics, textiles and papermaking, etc., can solve the problems of uneven cross-section, difficult transverse tearing, inconvenient use, etc., and achieve the effect of flat cross-section.
- Summary
- Abstract
- Description
- Claims
- Application Information
AI Technical Summary
Problems solved by technology
Method used
Image
Examples
Embodiment 1
[0013] Get the model that Shanghai petrochemical company produces is the polypropylene chip (particle) 98 weight parts of Y37007, mix into brown color masterbatch chip (particle) 2 weight parts, and add 2 weight parts antioxidant 1010 and 1 weight part photostable Agent UV-327, mixed evenly, sucked into the screw extruder by the vacuum feeding system, controlled the temperature between 225-230°C, melted and extruded the polymer, the melt was filtered by a filter, metered by a metering pump, and then sprayed The plate is sprayed into filaments, the temperature of the spinneret is controlled between 200-250°C, and the spinning speed is controlled between 3500-4000m / min. Then, the ejected silk is introduced into the air duct, blown and cooled by side blowing, and the blowing speed is set between 0.8-1.0m / s. After the cooled filaments are drafted by the drafting machine, they are guided by the carding machine to move back and forth on the transmission net that is at right angles t...
Embodiment 2
[0015] Get the model produced by Shanghai Petrochemical Company as 95 parts by weight of polypropylene slices (particles) of Y37007, add 5 parts by weight of deep blue color masterbatch chips (particles), and add 3 parts by weight of antioxidant 1076, mix them by vacuum The material system is sucked into the screw extruder, and the temperature is controlled between 230-235°C to melt and extrude the polymer. The melt is filtered through a filter, metered by a metering pump, and then sprayed out through the spinneret to form filaments, and the spinneret spins The temperature is controlled between 250-300°C, and the spinning speed is controlled between 4000-4500m / min. Then, the ejected silk is introduced into the air duct, and is blown and cooled by side blowing, and the blowing speed is set between 1.4-1.6m / s. After the cooled filaments are drafted by the drafting machine, they are guided by the carding machine to move back and forth on the transmission net that is at right angl...
Embodiment 3
[0017] Take 99 parts by weight of polyester chips or nylon chips, add 1 part by weight of white masterbatch chips (particles), and add 2 parts by weight of light stabilizer UV-327, after mixing, suck it into the screw extruder by the vacuum feeding system , control the temperature between 228-232°C, melt and extrude the polymer, the melt is filtered through a filter, metered by a metering pump, and then sprayed out through a spinneret to form filaments, and the temperature of the spinneret is controlled at 250-280°C Between, the spinning speed is controlled between 3500-4000m / min. Then, the ejected silk is introduced into the air duct, blown and cooled by side blowing, and the blowing speed is set between 1.0-1.2m / s. After the cooled filaments are drafted by the drafting machine, they are guided by the carding machine to move back and forth on the transmission net that is at right angles to the carding machine, to lay and overlap, and to lay the semi-finished non-woven fabric ...
PUM
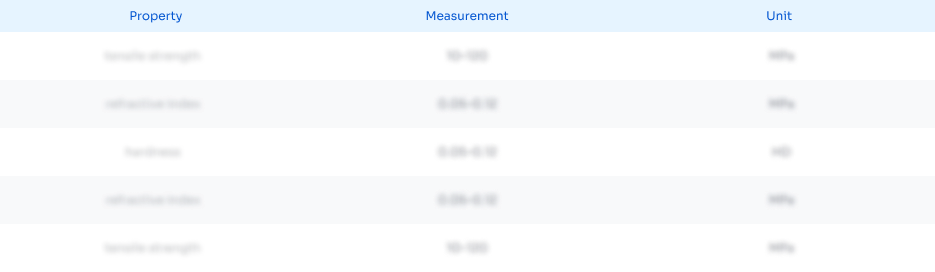
Abstract
Description
Claims
Application Information

- R&D Engineer
- R&D Manager
- IP Professional
- Industry Leading Data Capabilities
- Powerful AI technology
- Patent DNA Extraction
Browse by: Latest US Patents, China's latest patents, Technical Efficacy Thesaurus, Application Domain, Technology Topic, Popular Technical Reports.
© 2024 PatSnap. All rights reserved.Legal|Privacy policy|Modern Slavery Act Transparency Statement|Sitemap|About US| Contact US: help@patsnap.com