Composite resin plate
A technology of resin composite and board, applied in the field of composite board manufacturing, can solve the problems of poor tensile resistance, waterproof and wear resistance, loose particles, low internal bonding strength, etc., to achieve sanitation and good tensile resistance. and wear resistance
- Summary
- Abstract
- Description
- Claims
- Application Information
AI Technical Summary
Problems solved by technology
Method used
Image
Examples
Embodiment 1
[0041] A resin composite plate, comprising the following raw materials in weight percentage: 30-50% of plastic powder, 40-55% of resin fiber powder, 4-22% of butadiene rubber, 3-5% of fiber adhesive, and 0.2% of triphenyl phosphite ~0.4%.
[0042] To achieve the best effect of the board, the percentage by weight of each raw material should be kept as follows: 30% of plastic powder, 50% of resin fiber powder, 14.6% of butadiene rubber, 5% of fiber cement, and 0.4% of triphenyl phosphite.
[0043] Production method: In this embodiment, resin fiber powder is used as the main raw material, plastic powder is added as the auxiliary raw material, the two powders are dried separately and then fully mixed, then the butadiene rubber adhesive, fiber adhesive and modifier sub Triphenyl phosphate, after fully mixing the powders, place them in a mold with a gauge pressure of 10KPa to 20Kpa at 190°C to 250°C for compression molding, and the formed boards are glued with butadiene glue and fib...
Embodiment 2
[0049] A resin composite plate, comprising the following raw materials in weight percentage: 20-30% of plastic powder, 50-70% of resin fiber powder, 7-20% of adhesive, and 2-15% of modifier; the adhesive is phenolic Resin, described modifying agent is the mixture of aluminum hydroxide, calcium stearate, nano calcium carbonate.
[0050] The optimum weight percentages of the above raw materials are: 20% of plastic powder, 50% of resin fiber powder, 15% of phenolic resin, 4% of aluminum hydroxide, 3% of calcium stearate and 8% of nanometer calcium carbonate.
[0051] In this embodiment, the modifier calcium stearate and nano-calcium carbonate are used to effectively increase the toughness of the board and prevent the board from being crushed due to excessive rigidity, and the nano-calcium carbonate is used as a fine filler to effectively fill the plastic powder and The gap between the resin fiber powder makes the board bonding effect better and can form a smooth surface on the bo...
Embodiment 3
[0054] A resin composite board, comprising the following raw materials in weight percentage: 20-30% of plastic powder, 30-50% of resin fiber powder, 8-25% of adhesive, and 15-20% of modifier; the adhesive is phenolic Resin, described modifying agent is wood fiber powder.
[0055] The optimum weight percentages of the above raw materials are: 20% of plastic powder, 50% of resin fiber powder, 15% of phenolic resin and 15% of wood fiber powder.
[0056] Its production method is as shown in Example 1.
[0057] Also can adopt following percentage by weight in order to reach better effect in the present embodiment: plastic powder 30%, resin fiber powder 30%, phenolic acid resin 25%, wood fiber powder 15%; Or be: plastic powder 25% %, resin fiber powder 47%, phenolic resin 8%, wood fiber powder 20%.
PUM
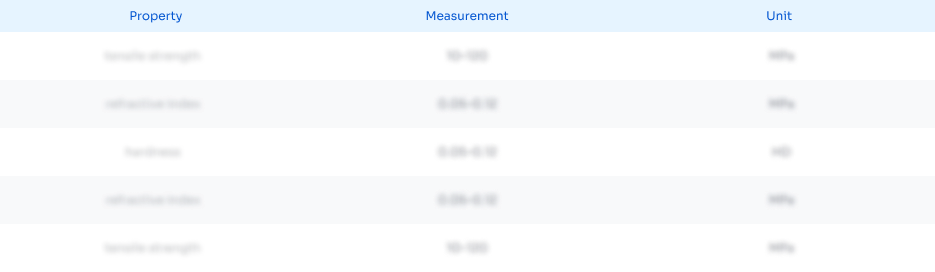
Abstract
Description
Claims
Application Information

- Generate Ideas
- Intellectual Property
- Life Sciences
- Materials
- Tech Scout
- Unparalleled Data Quality
- Higher Quality Content
- 60% Fewer Hallucinations
Browse by: Latest US Patents, China's latest patents, Technical Efficacy Thesaurus, Application Domain, Technology Topic, Popular Technical Reports.
© 2025 PatSnap. All rights reserved.Legal|Privacy policy|Modern Slavery Act Transparency Statement|Sitemap|About US| Contact US: help@patsnap.com