Modular Transportable System For SAGD Process
a transportable system and modular technology, applied in the direction of insulation, drilling pipes, borehole/well accessories, etc., can solve the problems of long interconnection pipelines, large capital injections, and facilities that have demonstrated very unreliable results
- Summary
- Abstract
- Description
- Claims
- Application Information
AI Technical Summary
Benefits of technology
Problems solved by technology
Method used
Image
Examples
Embodiment Construction
[0110]KemeX has developed a new SAGD plant design that achieves the following:[0111]a) Plant capacity and size reduced to fit business needs and improves economics[0112]b) Lower capital and operating costs per unit of production[0113]c) Increased plant reliability[0114]d) Reduced environmental footprint[0115]e) Extended facility life through portability
Key Design Features and Benefits
[0116]The plant design that was created focused on addressing the critical factors influencing future oil n sands exploitation needs. Key features of the KemeX 1n Site / UltraLite SAGD plant design include:[0117]Modular / Portable design[0118]Lower capital cost[0119]Lower operating costs[0120]Smaller capacity[0121]Lower environmental impact[0122]Higher water recycle rate[0123]High energy efficiency[0124]Lower emissions[0125]Minimal land disturbance[0126]Shorter project schedule
Modular / Portable
[0127]The modular / portable concept provides some distinct advantages:[0128]Minimizes the site labour requirement, th...
PUM
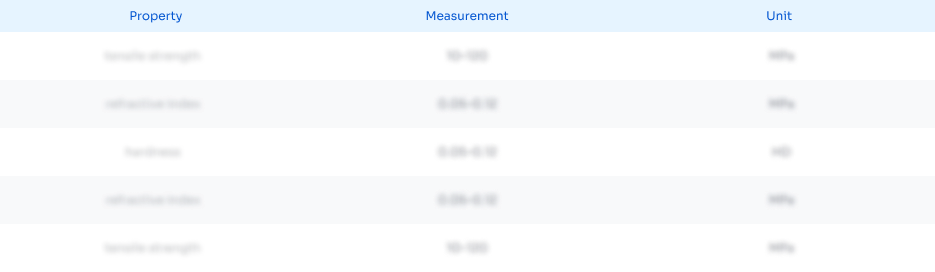
Abstract
Description
Claims
Application Information

- Generate Ideas
- Intellectual Property
- Life Sciences
- Materials
- Tech Scout
- Unparalleled Data Quality
- Higher Quality Content
- 60% Fewer Hallucinations
Browse by: Latest US Patents, China's latest patents, Technical Efficacy Thesaurus, Application Domain, Technology Topic, Popular Technical Reports.
© 2025 PatSnap. All rights reserved.Legal|Privacy policy|Modern Slavery Act Transparency Statement|Sitemap|About US| Contact US: help@patsnap.com