Casing shoes including cutting elements, cutting elements for earth-boring tool, and related methods
a cutting element and cutting element technology, applied in the direction of drilling rods, drilling pipes, cutting machines, etc., can solve the problems of high cost, high cost of operation, and time-consuming sequence drilling and casing, so as to facilitate drilling, reduce damage, and high resistance
- Summary
- Abstract
- Description
- Claims
- Application Information
AI Technical Summary
Benefits of technology
Problems solved by technology
Method used
Image
Examples
Embodiment Construction
[0110]FIGS. 1A-1D illustrate a casing bit 12 according to the present invention. As shown in FIG. 1A, casing bit 12 includes a nose portion 20 and generally radially extending blades 22, forming fluid courses 24 therebetween extending to junk slots 35 between circumferentially adjacent blades 22. Blades 22 may also include pockets 30, which may be configured to carry cutting elements (not shown), such as, for instance, polycrystalline diamond cutting elements. Generally, a cutting element may comprise a superabrasive region that is bonded to a substrate. A particular cutting element that is used in rotary drill bits is a polycrystalline diamond compact (“PDC”) cutter. Rotary drag bits employing PDC cutters have been employed for several decades. PDC cutters are typically comprised of a disc-shaped diamond “table” formed on and bonded under a high-pressure and high-temperature (HPHT) process to a supporting substrate such as cemented tungsten carbide (WC), although other configuratio...
PUM
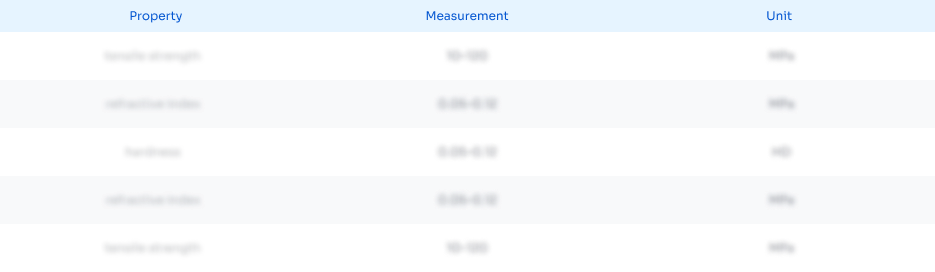
Abstract
Description
Claims
Application Information

- R&D Engineer
- R&D Manager
- IP Professional
- Industry Leading Data Capabilities
- Powerful AI technology
- Patent DNA Extraction
Browse by: Latest US Patents, China's latest patents, Technical Efficacy Thesaurus, Application Domain, Technology Topic, Popular Technical Reports.
© 2024 PatSnap. All rights reserved.Legal|Privacy policy|Modern Slavery Act Transparency Statement|Sitemap|About US| Contact US: help@patsnap.com