Method for fabricating semiconductor device
a manufacturing method and semiconductor technology, applied in the direction of manufacturing tools, fine working devices, electric devices, etc., can solve the problem of the size of the semiconductor chips to be singulated from the semiconductor wafers becoming smaller, and achieve the effect of improving the manufacturing yield and decreasing the manufacturing yield
- Summary
- Abstract
- Description
- Claims
- Application Information
AI Technical Summary
Benefits of technology
Problems solved by technology
Method used
Image
Examples
first embodiment
[0078]In a first embodiment, a method of manufacturing a Liquid Crystal Display (LCD) driver (semiconductor device) for use in a liquid-crystal display apparatus is described.
[0079]First, on a chip area of a semiconductor wafer with a substantially disk shape, a circuit element, such as Metal Insulator Semiconductor Field Effect Transistor (MISFET), is formed by using a well-known technology. Then, on an upper layer of the MISFET formed on the semiconductor wafer, a multilayer interconnection is formed. The multilayer interconnection is formed of, for example, metal wiring made of, for example, an aluminum film or an aluminum-alloy film with aluminum as a base metal, through an inter-layer insulating film composed of, for example, a silicon oxide film. Also, part or approximately all of layers forming the multilayer interconnections may be formed of copper films or films with copper as a base metal (damascene interconnection). Then, on the multilayer interconnection, a bump electrod...
second embodiment
[0139]In the first embodiment, the example has been described in which the dicing line group in the vertical direction and the dicing line group in the horizontal direction are both formed through the step-cutting. In a second embodiment, an example is described in which either one of the dicing line groups in the vertical or horizontal directions (second dicing line group) is formed through the single-cutting, while the other dicing line group (first dicing line group) is formed through the step-cutting.
[0140]FIG. 42 is a plan view showing the semiconductor wafer 3 to which dicing according to the second embodiment is performed. As shown in FIG. 42, semiconductor chips are for use in an LCD driver, and it can be seen that conforming chip area has a rectangular shape.
[0141]FIG. 43 is an enlarged plan view of a vicinity of the outer periphery 14 of the semiconductor wafer 3, and a plan view of an element formation surface (front surface) of the semiconductor wafer 3. FIG. 44 is an en...
PUM
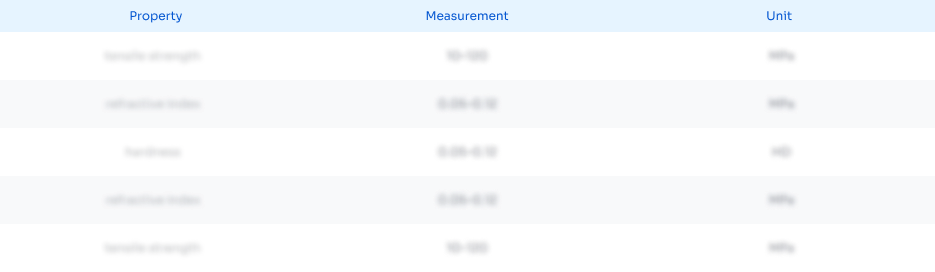
Abstract
Description
Claims
Application Information

- R&D
- Intellectual Property
- Life Sciences
- Materials
- Tech Scout
- Unparalleled Data Quality
- Higher Quality Content
- 60% Fewer Hallucinations
Browse by: Latest US Patents, China's latest patents, Technical Efficacy Thesaurus, Application Domain, Technology Topic, Popular Technical Reports.
© 2025 PatSnap. All rights reserved.Legal|Privacy policy|Modern Slavery Act Transparency Statement|Sitemap|About US| Contact US: help@patsnap.com