High efficiency radiant burner
- Summary
- Abstract
- Description
- Claims
- Application Information
AI Technical Summary
Benefits of technology
Problems solved by technology
Method used
Image
Examples
Embodiment Construction
[0024]The following discussion is presented to enable a person skilled in the art to make and use the invention. Various modifications to the preferred embodiments will be readily apparent to those skilled in the art, and the generic principles herein may be applied to other embodiments and applications without departing from the spirit and scope of the present invention as defined by the appended claims. Thus, the present invention is not intended to be limited to the embodiments show, but is to be accorded the widest scope consistent with the principles and features disclosed herein.
[0025]Unless otherwise noted herein, most parts of burner 10 and heat exchanger 90 are constructed from metal. Depending upon the part's application, the metal may be aluminum, steel, copper, brass or similar conventional metal. The selection of metal is primarily driven by thermal transfer considerations, although resistances to corrosion and high temperatures, as well as weight considerations are als...
PUM
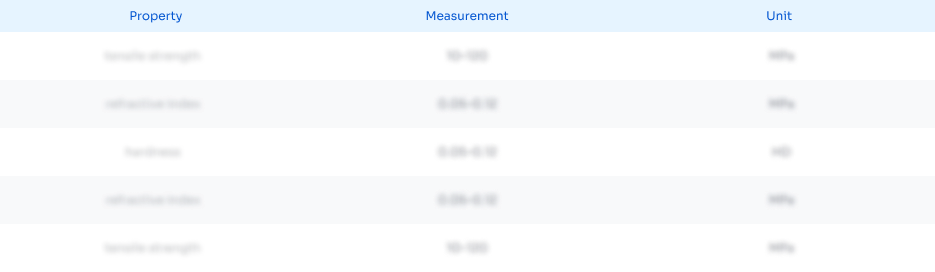
Abstract
Description
Claims
Application Information

- R&D
- Intellectual Property
- Life Sciences
- Materials
- Tech Scout
- Unparalleled Data Quality
- Higher Quality Content
- 60% Fewer Hallucinations
Browse by: Latest US Patents, China's latest patents, Technical Efficacy Thesaurus, Application Domain, Technology Topic, Popular Technical Reports.
© 2025 PatSnap. All rights reserved.Legal|Privacy policy|Modern Slavery Act Transparency Statement|Sitemap|About US| Contact US: help@patsnap.com