Low-melting point superabrasive tools and associated methods
a superabrasive tool and low-melting point technology, applied in the direction of grinding device, abrasive surface conditioning device, metal-working apparatus, etc., can solve the problems of abrasive slurry, abrasive dust coming from workpieces, and the accumulation of polishing debris coming from workpieces, so as to achieve the effect of improving the wetting and low-melting poin
- Summary
- Abstract
- Description
- Claims
- Application Information
AI Technical Summary
Benefits of technology
Problems solved by technology
Method used
Image
Examples
Embodiment Construction
[0025]Definitions
[0026]In describing and claiming the present invention, the following terminology will be used in accordance with the definitions set forth below.
[0027]The singular forms “a,”“an,” and, “the” include plural referents unless the context clearly dictates otherwise. Thus, for example, reference to “a particle” includes reference to one or more of such particles, and reference to “the reactive material” includes reference to one or more of such materials.
[0028]As used herein, “superhard” and “superabrasive” may be used interchangeably, and refer to a crystalline, or polycrystalline material, or mixture of such materials having a Vicker's hardness of about 4000 Kg / mm2 or greater. Such materials may include without limitation, diamond, and cubic boron nitride (cBN), as well as other materials known to those skilled in the art. While superabrasive materials are very inert and thus difficult to form chemical bonds with, it is known that certain reactive elements, such as ch...
PUM
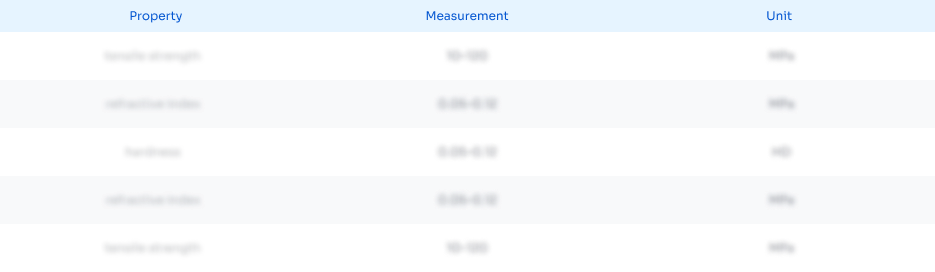
Abstract
Description
Claims
Application Information

- R&D
- Intellectual Property
- Life Sciences
- Materials
- Tech Scout
- Unparalleled Data Quality
- Higher Quality Content
- 60% Fewer Hallucinations
Browse by: Latest US Patents, China's latest patents, Technical Efficacy Thesaurus, Application Domain, Technology Topic, Popular Technical Reports.
© 2025 PatSnap. All rights reserved.Legal|Privacy policy|Modern Slavery Act Transparency Statement|Sitemap|About US| Contact US: help@patsnap.com