Method for high energy density biomass-water slurry
- Summary
- Abstract
- Description
- Claims
- Application Information
AI Technical Summary
Benefits of technology
Problems solved by technology
Method used
Image
Examples
example 1
[0025]Referring to FIG. 1, a mixture of 50% biomass, consisting of pine tree particles in water is shown before treatment. Dry pine sawdust was obtained from American Wood Fibers and the dry White Cedar from Utah. The sawdust was ground using a commercially available coffee grinder and sieved to <100 mesh (150 μm). For the wood pre-treatment, an autoclave system was set up. It consisted of an Autoclave Engineers EZE-Seal pressure vessel rated at 3,300 psi at 850° F. The wood sample and deionized water were weighed and then well mixed by hand to even water distribution in a large beaker before putting it in the vessel. The amount of wood added was adjusted for moisture content. The vessel was then weighed with contents, vacuumed and purged three times with argon, and finally pressurized to 100±1 psi. The temperature was ramped to operating temperature (210-230° C.) in about 30 minutes and then held for 30 minutes. Pressure and internal temperature were recorded using a data acquisiti...
example 2
[0027]The procedure of Example 1 was followed but the vessel was preheated to >200° C. before being put in the heater. The autoclave was found to reach 230° C. in 15 minutes or less and then it was held for 30 minutes. The time needed to reach the target temperature did not have a noticeable physical impact on the resulting product
example 3
[0028]The method of Example 1 can be carried out but in which the starting mixture is non-pumpable agricultural waste containing 60 weight percent solids. The result will be a pumpable slurry containing 60 wt. % solids in water.
PUM
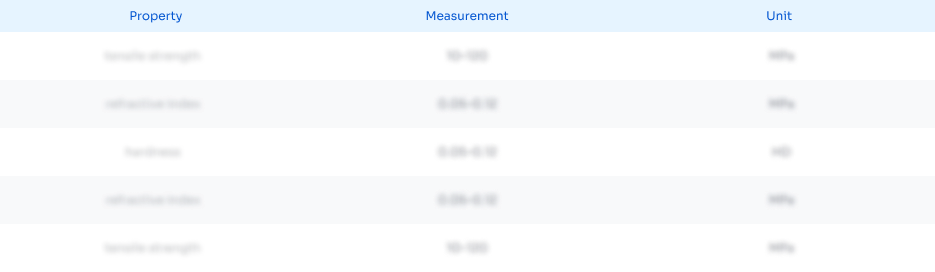
Abstract
Description
Claims
Application Information

- R&D
- Intellectual Property
- Life Sciences
- Materials
- Tech Scout
- Unparalleled Data Quality
- Higher Quality Content
- 60% Fewer Hallucinations
Browse by: Latest US Patents, China's latest patents, Technical Efficacy Thesaurus, Application Domain, Technology Topic, Popular Technical Reports.
© 2025 PatSnap. All rights reserved.Legal|Privacy policy|Modern Slavery Act Transparency Statement|Sitemap|About US| Contact US: help@patsnap.com