Weight member for a golf club head
- Summary
- Abstract
- Description
- Claims
- Application Information
AI Technical Summary
Benefits of technology
Problems solved by technology
Method used
Image
Examples
Embodiment Construction
[0015] A preferred embodiment of the present invention is now to be described hereinafter in detail.
[0016] Referring initially to FIG. 1, a golf club head in accordance with the present invention includes a golf club head body 20 having a recession 21, and a weight member 10 engaged in the recession 21 of the golf club head body 20 by means of welding, insertion, pressing, or brazing. The shape of the weight member 10 and the location of the recession 21 can be altered according to the product need. The weight member 10 can be made by powder metallurgy.
[0017] In a case that the weight member is manufactured by a precision casting process, metals are fed into a high-temperature furnace at a temperature between 1450° C. and 1750° C. (preferably 1660° C.-1680° C.) in a specific metal melting sequence and a specific composition ratio while controlling the mixture ratio among tungsten, molybdenum, and nickel, thereby forming a molten WMoNi alloy. Next, the molten WMoNi alloy is poured ...
PUM
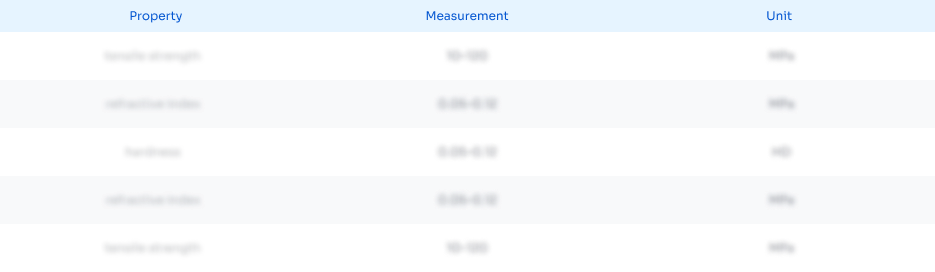
Abstract
Description
Claims
Application Information

- R&D
- Intellectual Property
- Life Sciences
- Materials
- Tech Scout
- Unparalleled Data Quality
- Higher Quality Content
- 60% Fewer Hallucinations
Browse by: Latest US Patents, China's latest patents, Technical Efficacy Thesaurus, Application Domain, Technology Topic, Popular Technical Reports.
© 2025 PatSnap. All rights reserved.Legal|Privacy policy|Modern Slavery Act Transparency Statement|Sitemap|About US| Contact US: help@patsnap.com