Self-stiffened welded wire lath assembly
a technology of welded wire and assembly, applied in the field of building technology, can solve the problems of stucco sag, underside of exposed roof area, difficulty in applying stucco to overhanging surfaces, etc., and achieve the effects of reducing blowing, reducing stress, and being more rigid
- Summary
- Abstract
- Description
- Claims
- Application Information
AI Technical Summary
Benefits of technology
Problems solved by technology
Method used
Image
Examples
Embodiment Construction
[0045] Throughout the following description, specific details are set forth in order to provide a more thorough understanding of the invention. However, the invention may be practiced without some of these particulars. In other instances, well known elements have not been shown or described in detail to avoid unnecessarily obscuring the invention. Accordingly, the specification and drawings are to be regarded in an illustrative, rather than a restrictive, sense.
[0046] Referring to FIG. 2 and FIG. 3, lath 10 according to a currently preferred embodiment of the invention comprises a plurality of first generally parallel longitudinal wires 12 which intersect with a plurality of generally parallel transverse wires 14.
[0047] Wires 12 lie substantially in a first plane PI (best appreciated by reference to FIG. 3). Similarly, wires 14 lie substantially in plane PI, save that wires 14 are bent out of plane P1 at truss locations 15.
[0048] Wires 12 and 14 are welded together at their inter...
PUM
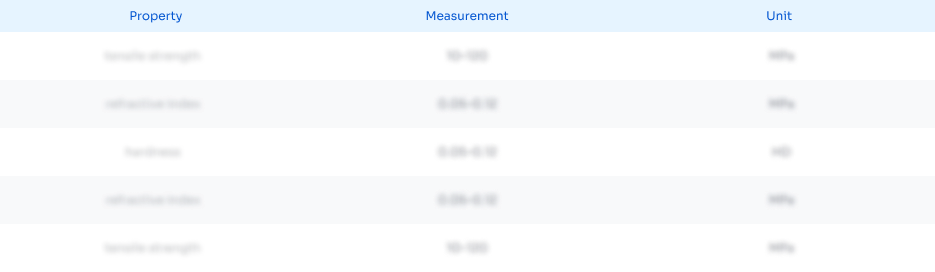
Abstract
Description
Claims
Application Information

- R&D
- Intellectual Property
- Life Sciences
- Materials
- Tech Scout
- Unparalleled Data Quality
- Higher Quality Content
- 60% Fewer Hallucinations
Browse by: Latest US Patents, China's latest patents, Technical Efficacy Thesaurus, Application Domain, Technology Topic, Popular Technical Reports.
© 2025 PatSnap. All rights reserved.Legal|Privacy policy|Modern Slavery Act Transparency Statement|Sitemap|About US| Contact US: help@patsnap.com