Method for reducing waste oxide gas emissions in industrial processes
a waste oxide gas and industrial process technology, applied in the field of new waste gas oxide gas emission reduction methods, can solve the problems of waste oxide gas producing undesirable effects, accelerating corrosion of buildings and monuments, and destroying waste, so as to reduce emissions, enhance destruction efficiency, and maximize residence time
- Summary
- Abstract
- Description
- Claims
- Application Information
AI Technical Summary
Benefits of technology
Problems solved by technology
Method used
Image
Examples
example 1
[0063] In an industrial chemical process for making acrylic acid from propylene feed, a horizontal three stage thermal oxidizer of the type illustrated in FIG. 1 was employed to dispose of waste streams. The furnace section of the thermal oxidizer (from addition point 21 to the end of waste destruction zone 26) was approximately 15.9 meters (52 feet) long. The inside diameter of primary waste destruction zone 24 was 1.8 meters (6 feet) and the inside diameter of secondary waste destruction zone 26 was 3.2 meters (10.5 feet). The base load NOx emissions for the thermal oxidizer were determined as follows:
[0064] Natural Gas from a commercial pipeline was used as the combustion fuel stream 12 and was injected into the primary combustion zone at a rate of 24, 525 liters / minute (866 scfm). Ambient temperature atmospheric air was used for oxidant stream 10. The airflow was injected into the primary combustion zone 22 at a rate of 310,387 liters / minute (10,960 scfm) and into the secondary ...
PUM
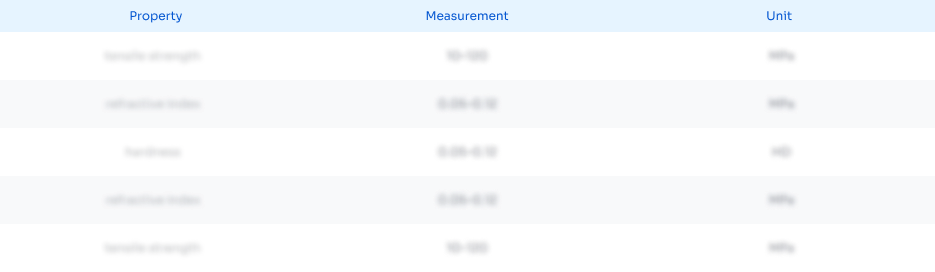
Abstract
Description
Claims
Application Information

- R&D
- Intellectual Property
- Life Sciences
- Materials
- Tech Scout
- Unparalleled Data Quality
- Higher Quality Content
- 60% Fewer Hallucinations
Browse by: Latest US Patents, China's latest patents, Technical Efficacy Thesaurus, Application Domain, Technology Topic, Popular Technical Reports.
© 2025 PatSnap. All rights reserved.Legal|Privacy policy|Modern Slavery Act Transparency Statement|Sitemap|About US| Contact US: help@patsnap.com