Hybric organic resin film and its prepn process
A technology of organic membranes and resins, applied in the field of functional separation membranes and their preparation, can solve the problems of easy deactivation of functional groups, complicated polymerization methods, and difficult synthesis, and achieve the effects of fast process speed, wide source of raw materials, and simple methods
- Summary
- Abstract
- Description
- Claims
- Application Information
AI Technical Summary
Problems solved by technology
Method used
Image
Examples
preparation example Construction
[0029] The present invention simultaneously designs the preparation method of described hybrid film, and it comprises the following steps:
[0030] 1. Preparation of casting solution: According to the mass percentage requirements of the hybrid film formula of the present invention, fully mix the various components described, stir at 70-80°C for 4-12 hours, and stand at room temperature for defoaming After 24 to 48 hours, a uniformly mixed casting solution is obtained;
[0031] 2. Membrane making: At 20-90°C, scrape-coat the prepared casting solution on a flat plate or non-woven fabric to form a flat film, and then soak it in a coagulation bath with a temperature of 20-90°C for 48-48°C. 72 hours, so that the film is solidified and formed completely, and the residual solvent and additives are removed, and the resin hybrid organic film with adsorption function can be prepared. The flat plate includes a flat glass plate and a stainless steel plate; the scraping method can be scra...
Embodiment 1
[0041] The mass percentage formula design of the hybrid membrane casting solution is: 14wt% polyethersulfone [BASF production]; 6wt% cation exchange resin powder [Nankai University chemical plant, model D061] (PES / resin=70 / 30), average particle size Diameter 10 μm; 20 wt% polyethylene glycol 400 (PEG-400); 2 wt% polyvinylpyrrolidone and 58 wt% N-methylpyrrolidone.
[0042] The process of manufacturing the hybrid film is: first add 6g resin to 58g NMP and stir, after the dispersion is complete, add 20gPE6-400 and 4gPVP, after the solid is completely dissolved, add 14g PES three times to ensure that the resin is dispersed in the polymer Completely, add PES and stir the solution at 70°C for 8 hours; after the dissolution and dispersion are complete, let it stand for defoaming for 24 hours to prepare a casting solution; manually scrape the casting solution at a temperature of 60°C on a glass plate After forming a flat film with a thickness of 0.25mm, solidify and form it in a wate...
Embodiment 2
[0044] The formula design of all mass percentages of the hybrid film casting solution is: 14wt% polyethersulfone [BASF production]; 20wt% cation exchange resin powder [Nankai University chemical plant, model D061] (PES / resin=41 / 59), average Particle size 10 μm; 20 wt% polyethylene glycol 400; 2 wt% polyvinylpyrrolidone and 44 wt% N-methylpyrrolidone.
[0045] The process of manufacturing the hybrid film is as follows: first add 20g of resin to 44g of NMP and stir, after the dispersion is complete, add 20g of PEG-400 and 2g of PVP, and after the solid is completely dissolved, add 14g of PES in three times to ensure that the resin is completely dispersed in the polymer. After adding PES, stir the solution at 80°C for 4 hours; after the dissolution and dispersion are complete, let it stand for defoaming for 24 hours to prepare a casting solution; manually scrape the casting solution at a temperature of 60°C on a glass plate to make a thickness After forming a flat film of 0.25 mm...
PUM
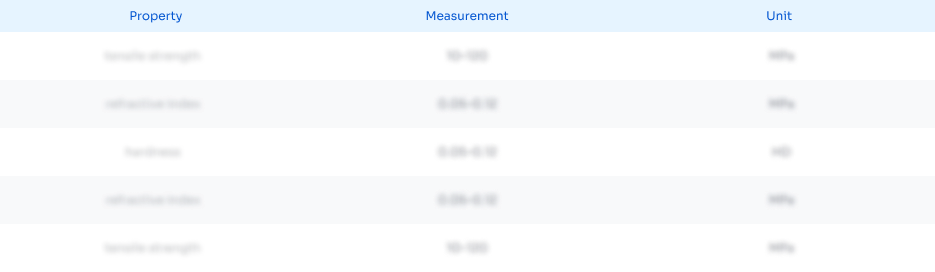
Abstract
Description
Claims
Application Information

- Generate Ideas
- Intellectual Property
- Life Sciences
- Materials
- Tech Scout
- Unparalleled Data Quality
- Higher Quality Content
- 60% Fewer Hallucinations
Browse by: Latest US Patents, China's latest patents, Technical Efficacy Thesaurus, Application Domain, Technology Topic, Popular Technical Reports.
© 2025 PatSnap. All rights reserved.Legal|Privacy policy|Modern Slavery Act Transparency Statement|Sitemap|About US| Contact US: help@patsnap.com