Manufacturing process of self-aligned silicide barrier layer
A self-aligned silicide and manufacturing process technology, applied in semiconductor/solid-state device manufacturing, electrical components, circuits, etc., can solve problems such as reducing leakage current and filling capacity
- Summary
- Abstract
- Description
- Claims
- Application Information
AI Technical Summary
Problems solved by technology
Method used
Image
Examples
Embodiment Construction
[0012] As shown in Figure 3, the existing salicide barrier layer growth process method includes the following steps: using PECVD (plasma enhanced chemical vapor deposition) to grow a layer of silicon dioxide, glue, self-aligned insoluble Mask the metal silicide barrier layer (SAB), perform HF (hydrofluoric acid) etching, and grow a self-aligned refractory metal silicide (Salicide) layer.
[0013] The self-aligned silicide barrier layer growth process of the present invention is shown in Figure 4, and it includes the following steps: growing the first layer of silicon dioxide by CVD, and regrowing the second layer of silicon dioxide on the first layer of silicon dioxide by HDP. Layer silicon dioxide, glue coating, SAB mask plate photomask, perform HF etching, and grow Salicide layer.
[0014] The process flow of the present invention is the same as the existing process flow. At first, a layer of silicon dioxide is grown by CVD, but the first layer of silicon dioxide grown by th...
PUM
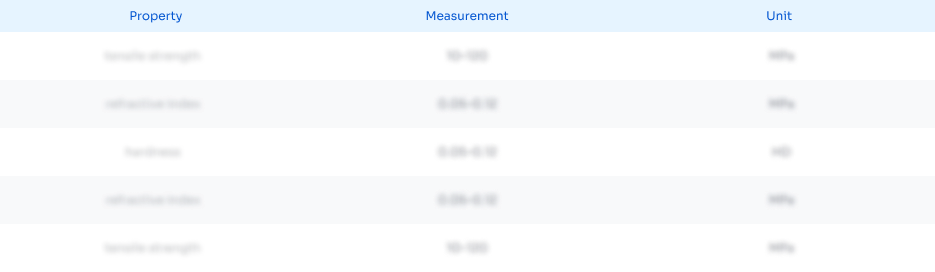
Abstract
Description
Claims
Application Information

- R&D
- Intellectual Property
- Life Sciences
- Materials
- Tech Scout
- Unparalleled Data Quality
- Higher Quality Content
- 60% Fewer Hallucinations
Browse by: Latest US Patents, China's latest patents, Technical Efficacy Thesaurus, Application Domain, Technology Topic, Popular Technical Reports.
© 2025 PatSnap. All rights reserved.Legal|Privacy policy|Modern Slavery Act Transparency Statement|Sitemap|About US| Contact US: help@patsnap.com