Method for treating converter flue gas
A technology for converter flue gas and a treatment method, which is applied in the field of converter flue gas treatment, can solve the problems of large water consumption, difficult treatment and utilization of sludge, water pollution, etc., and achieves improved gas quality, good environmental protection effect, and water resource conservation. Effect
- Summary
- Abstract
- Description
- Claims
- Application Information
AI Technical Summary
Problems solved by technology
Method used
Image
Examples
Embodiment Construction
[0010] In the figure, 1 represents the converter, 2 represents the movable hood of the converter, 3 represents the waste heat boiler, 4 represents the gravity settling chamber, 5 represents the flue gas pipeline, 6 represents the high-efficiency inorganic heat pipe heat exchanger, 7 represents the bag filter, 8 represents the induction Fan, 9 represents gas component detection device, 10 represents switching station, 11 represents gas recovery pipe, 12 represents discharge chimney.
[0011] The steps of the method of the present invention are as follows: the flue gas produced by the converter 1 is captured by the movable hood 2 and enters the waste heat boiler 3. The waste heat boiler 3 is essentially a heat exchanger, and the converter flue gas The temperature drops to around 1000°C (~550°C). Then enter the gravity settling chamber 4 to remove 25~35% coarse dust (≥40um) particles. After that, the flue gas enters the high-efficiency inorganic heat pipe heat exchanger 6 throug...
PUM
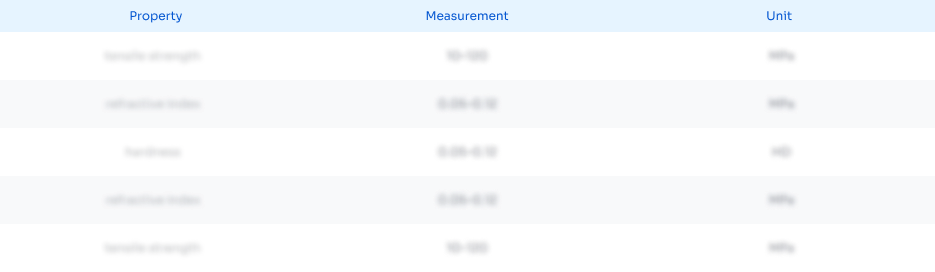
Abstract
Description
Claims
Application Information

- R&D
- Intellectual Property
- Life Sciences
- Materials
- Tech Scout
- Unparalleled Data Quality
- Higher Quality Content
- 60% Fewer Hallucinations
Browse by: Latest US Patents, China's latest patents, Technical Efficacy Thesaurus, Application Domain, Technology Topic, Popular Technical Reports.
© 2025 PatSnap. All rights reserved.Legal|Privacy policy|Modern Slavery Act Transparency Statement|Sitemap|About US| Contact US: help@patsnap.com