Catalyst in use for polymerization or combined polymerization of ethylene, preparation and application
An ethylene polymerization and catalyst technology, applied in the field of catalysts for ethylene polymerization or copolymerization, can solve problems such as low content of active components, influence on polymerization activity, and easy breakage of catalysts.
- Summary
- Abstract
- Description
- Claims
- Application Information
AI Technical Summary
Problems solved by technology
Method used
Image
Examples
Embodiment 1
[0043] a) preparation of magnesium chloride mother liquor for spraying: after passing through N 2Add 600ml of dehydrated ethanol to the fully replaced stirred 1000ml reactor, and add 51g of anhydrous magnesium chloride while stirring at room temperature, control the adding speed of magnesium chloride, and keep the system temperature below 40°C. , the temperature of the mixed system was raised to 70°C, and kept at this temperature for 4 hours to obtain a uniform MgCl 2 ethanol solution. Add 25.5g of smoky silica gel into the above solution under the condition of rapid stirring, continue to maintain the original temperature and stir rapidly for more than 1.5 hours, and obtain the mother liquor for spraying for later use.
[0044] b) Preparation of MgCl by spray drying 2 / SiO 2 Composite carrier: use a peristaltic pump to introduce the mother liquor obtained in step a) into a two-fluid nozzle through a pipeline, and atomize it into the drying chamber. Control feed liquid and ...
Embodiment 2
[0046] (1) Preparation of catalyst solid components
[0047] With a stirrer, through N 2 Add 100ml of hexane to the purified 250mL glass reactor. Under the condition of continuous stirring, the MgCl obtained in Example 1 2 / SiO 2 7g of the composite carrier was added therein, and after dispersing at room temperature for 30 minutes, 3ml of dry and purified ethanol was slowly added dropwise. After the dropwise addition, the stirring was continued for 3 hours. At room temperature, 23.4 ml of a 2.2M monochlorodiethylaluminum hexane solution was slowly added dropwise. After the dropwise addition, the temperature was raised to 35° C., and the mixture was stirred and reacted at a constant temperature of 35° C. for 2 hours. Then 13 ml of titanium tetrachloride was added dropwise, and after the addition of titanium tetrachloride was completed, the temperature was raised to 65° C. and then stirred at a constant temperature of 65° C. for 2 hours. Filter and wash four times, each wash...
Embodiment 3
[0051] (1) The synthesis of catalyst is the same as in Example 2. Only the amount of ethanol was changed from 3ml to 6ml; the amount of diethylaluminum hexane solution was changed from 23.4mL to 34ml.
[0052] (2) Ethylene polymerization is the same as embodiment 2.
PUM
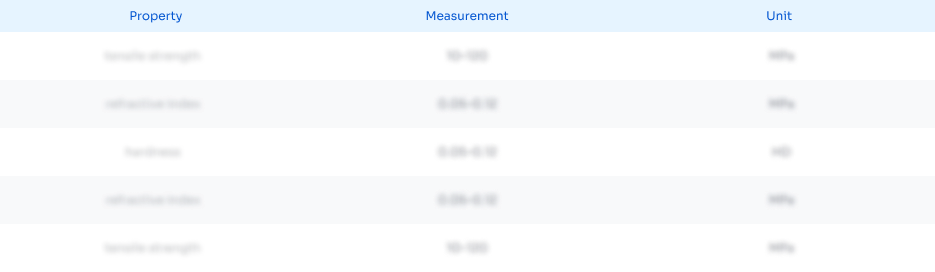
Abstract
Description
Claims
Application Information

- R&D Engineer
- R&D Manager
- IP Professional
- Industry Leading Data Capabilities
- Powerful AI technology
- Patent DNA Extraction
Browse by: Latest US Patents, China's latest patents, Technical Efficacy Thesaurus, Application Domain, Technology Topic, Popular Technical Reports.
© 2024 PatSnap. All rights reserved.Legal|Privacy policy|Modern Slavery Act Transparency Statement|Sitemap|About US| Contact US: help@patsnap.com