Capping technology for electron beam physical gaseous phase deposition coating using strong flow pulse ionic beam
A technology of physical vapor deposition and high-current pulse, which is applied to coatings, electrical components, ion implantation plating, etc., can solve the problems of reducing thermal fatigue resistance of coatings, increasing the complexity and cost of capping process, and inducing stress concentration. Achieve the effects of improving thermal corrosion resistance, high temperature oxidation resistance and prolonging service life
- Summary
- Abstract
- Description
- Claims
- Application Information
AI Technical Summary
Problems solved by technology
Method used
Image
Examples
Embodiment 1
[0044] After an aero-engine company adopts electron beam physical vapor deposition coating on the blades of a gas turbine engine, it is required to form a 1 μm thick continuous tight top layer 7 on the surface of the ceramic layer 3, and the surface of the coating after treatment is required to be flat and smooth, so as to improve coating performance. The high temperature oxidation resistance and thermal shock performance of the layer. Now adopt the inventive method, its capping process step is as follows:
[0045] In the first step, the turbine blade is placed on the sample stage and vacuumized
[0046] Place the turbine blade with the deposited metal bonding layer and ceramic layer on the sample stage of the high-current pulsed ion beam device, so that the surface of the ceramic layer on the front surface of the blade is completely exposed to the high-current pulsed ion beam irradiation area, and close the The vacuum chamber of the device is evacuated, and its vacuum degree...
Embodiment 2
[0054] A company requires that the coated guide vane be capped, and a continuous tight sealing top layer 7 with a thickness of 3 μm is required to be formed on the surface of the ceramic layer 3 to improve the high temperature oxidation resistance of the guide vane, and the treated coating surface is required to be smooth. To reduce the resistance of the guide vanes to the gas, the method of the present invention is now adopted, and its capping process steps are as follows:
[0055] The first step is to place the guide vanes on the sample stage and vacuumize
[0056] Place the guide vane with deposited metal bonding layer and ceramic layer on the sample stage of the high-current pulsed ion beam device, so that the surface of the guide vane ceramic layer is completely exposed in the high-current pulsed ion beam irradiation area, and close the device The vacuum chamber is evacuated, and its vacuum degree reaches 1.0×10 -2 Pa.
[0057] The second step is to establish a capping ...
Embodiment 3
[0064] A diesel engine production unit wants to cap the coated diesel engine piston, and requires a continuous sealing top layer 7 with a thickness of 5 μm on the surface of the ceramic layer 3 to improve the high temperature oxidation resistance and thermal corrosion resistance of the piston. Chamber heat loss, now adopt the method of the present invention, its capping process steps are as follows:
[0065] The first step is to place the piston on the sample stage and vacuumize
[0066] Place the diesel engine piston with deposited metal bonding layer and ceramic layer on the sample stage of the high-current pulsed ion beam device, so that the surface of the piston ceramic layer is completely exposed in the high-current pulsed ion beam irradiation area, and close the device. The vacuum chamber is evacuated, and its vacuum degree reaches 8×10 -3 Pa.
[0067] The second step is to establish a capping layer on the surface of the piston ceramic layer
[0068] At room temperatu...
PUM
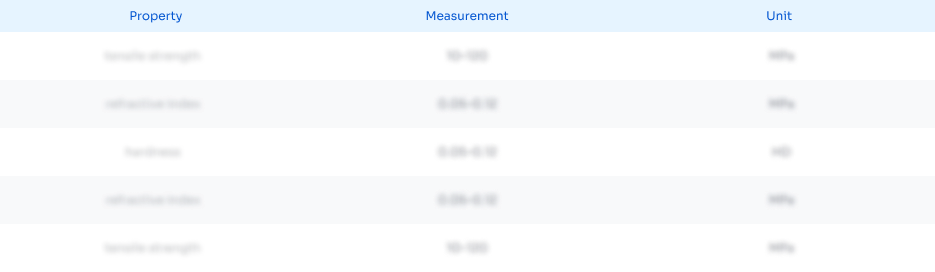
Abstract
Description
Claims
Application Information

- R&D
- Intellectual Property
- Life Sciences
- Materials
- Tech Scout
- Unparalleled Data Quality
- Higher Quality Content
- 60% Fewer Hallucinations
Browse by: Latest US Patents, China's latest patents, Technical Efficacy Thesaurus, Application Domain, Technology Topic, Popular Technical Reports.
© 2025 PatSnap. All rights reserved.Legal|Privacy policy|Modern Slavery Act Transparency Statement|Sitemap|About US| Contact US: help@patsnap.com