Yarn size producing method for textile warp
A production method and yarn pulp technology, applied in textiles, papermaking, fiber processing, etc., can solve the problems of strict technical requirements, poor permeability of yarn pulp, inability to adapt to multiple varieties, etc. The effect of facilitating the promotion of the application
- Summary
- Abstract
- Description
- Claims
- Application Information
AI Technical Summary
Problems solved by technology
Method used
Image
Examples
specific Embodiment approach 2
[0055] Carry out by specific implementation mode one, just:
[0056] The sizing of the operation step (2) is: select a kind of yarn pulp raw material (1).
[0057] Operational step (3) is selected as the method of heating and stirring, that is:
[0058] (3). A. Select the pulp raw material (1). A. After adding 300 kilograms of water 3 times the total weight of the pulp raw material described in the operation step (2), stirring evenly and completing the pulping, heat and Stirring, the temperature of heating and stirring is 45°C, and the time is 10 minutes;
[0059] The operation step (4) is: keep the temperature of 45° C. for the pulp prepared after the operation step (3).A.
specific Embodiment approach 3
[0060] Carry out by specific implementation mode one, just:
[0061] The sizing of operation step (2) is: select a kind of yarn pulp raw material (1).
[0062] Operational step (3) is selected as the method of heating and stirring, that is:
[0063] (3). A. Select yarn pulp raw material (1). A. After adding 350 kilograms of water of 3.5 times the total weight of yarn pulp raw material described in operation step (2), stirring evenly and completing the pulping, heat and Stirring, the temperature of heating and stirring is 50°C, and the time is 10 minutes;
[0064] The operation step (4) is: keep the temperature of 50° C. for the pulp prepared after the operation step (3).
specific Embodiment approach 4
[0065] Carry out by specific implementation mode one, just:
[0066] The sizing of the operation step (2) is: select a kind of yarn pulp raw material (1).
[0067] Operational step (3) is selected as the method of heating and stirring, that is:
[0068] (3). A. Select the pulp raw material (1). A. After adding 400 kilograms of water 4 times the total weight of the pulp raw material described in the operation step (2), stirring evenly and completing the pulping, heat and Stirring, the temperature of heating and stirring is 55° C., and the time is 10 minutes;
[0069] The operation step (4) is: keep the temperature of 55° C. for the pulp prepared after the operation step (3).A.
PUM
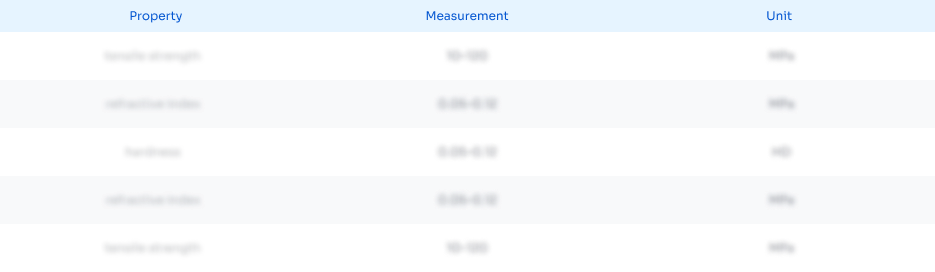
Abstract
Description
Claims
Application Information

- R&D Engineer
- R&D Manager
- IP Professional
- Industry Leading Data Capabilities
- Powerful AI technology
- Patent DNA Extraction
Browse by: Latest US Patents, China's latest patents, Technical Efficacy Thesaurus, Application Domain, Technology Topic, Popular Technical Reports.
© 2024 PatSnap. All rights reserved.Legal|Privacy policy|Modern Slavery Act Transparency Statement|Sitemap|About US| Contact US: help@patsnap.com