Method of preparing calcium propionate and calcium lactate with oyster shell as calcium source
A technology of oyster shells and calcium propionate, applied in carboxylate preparation, organic chemistry, etc., can solve the problems of high energy consumption, secondary pollution, and high cost, and achieve low energy consumption, low production cost, and low raw material purchase cost Effect
- Summary
- Abstract
- Description
- Claims
- Application Information
AI Technical Summary
Problems solved by technology
Method used
Examples
Embodiment 1
[0030] The oyster shells are washed, dried, and crushed to a fineness of less than 74 μm (through a 200-mesh sieve).
[0031] Add 50g of 200 mesh oyster shell powder and 200mL of water into a 2000mL three-neck flask, and add 670mL of propionic acid solution with a concentration of 10% in batches at 35°C under mechanical stirring (stirring speed is about 120r / min), and stir for 2.5h , with Ca(OH) 2 The pH of the reaction system was adjusted to about 9.0, and the reaction was continued for 1 h.
[0032] The reacted material was suction filtered under reduced pressure, and the filter residue was dried and weighed, and used as a raw material for re-feeding and reaction. The filtrate was concentrated to nearly dryness, and the crystals were dried at 80° C. to 85° C. for 4 hours to obtain 73 g of the product calcium propionate with a yield of 95%.
Embodiment 2
[0034] The oyster shells are scrubbed clean, dried, and crushed to a fineness of less than 154 μm (through a 100-mesh sieve).
[0035] Add 720g of 17% propionic acid solution into a 1000mL three-necked flask, and continuously add 100g of oyster shell powder with a fineness of 100 mesh at 20°C under mechanical stirring (stirring speed is about 140r / min), and stir for 1.5h. The pH of the reaction system was adjusted to about 8.0, and the reaction was continued for 1.5 h.
[0036] The reacted material was suction filtered under reduced pressure, and the filter residue was dried and weighed, and used as a raw material for re-feeding and reaction. The filtrate was concentrated to nearly dryness, and the crystals were dried at 100° C. to 105° C. for 2 hours to obtain 141 g of the product calcium propionate with a yield of 95%.
Embodiment 3
[0038] The oyster shells are scrubbed clean, dried, and crushed to a fineness of less than 100 μm.
[0039] Add 60kg and 260L of oyster shell powder into a 2000L stainless steel reaction kettle, add 800L of propionic acid solution with a concentration of 9% in batches at 50°C under mechanical stirring, stir for 2.5 hours, and use Ca(OH) 2 The pH of the reaction system was adjusted to about 8.0, and the reaction was continued for 1.5 h.
[0040] The reacted material is filtered under reduced pressure, and the filter residue is used as a raw material for re-feeding reaction. The filtrate was concentrated under reduced pressure to 20% (w / w), and the solution obtained was spray-dried (spray-drying conditions: feed concentration 20%, flow rate 30L / h, inlet temperature 200°C, outlet temperature 80°C), to obtain white calcium propionate Powder 85kg, finished product packaging is 25kg / bag.
PUM
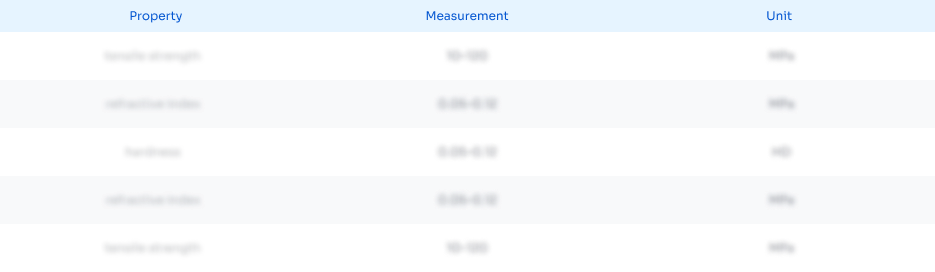
Abstract
Description
Claims
Application Information

- R&D Engineer
- R&D Manager
- IP Professional
- Industry Leading Data Capabilities
- Powerful AI technology
- Patent DNA Extraction
Browse by: Latest US Patents, China's latest patents, Technical Efficacy Thesaurus, Application Domain, Technology Topic, Popular Technical Reports.
© 2024 PatSnap. All rights reserved.Legal|Privacy policy|Modern Slavery Act Transparency Statement|Sitemap|About US| Contact US: help@patsnap.com