Method of producing high grade magnetic concentrate from sulfuric-acid residue composite pellet
A technology of magnetite concentrate and composite pellets, which is applied in the field of iron and steel metallurgy and can solve the problems of high impurity content, low dosage, and utilization rate of less than 50%.
- Summary
- Abstract
- Description
- Claims
- Application Information
AI Technical Summary
Problems solved by technology
Method used
Image
Examples
Embodiment 1
[0013] Embodiment 1: Additive formula (by weight): coal 70%, ferric chloride 10%, calcium carbonate 10%, sodium humate 10%. Additive dosage is 5%, sulfuric acid slag iron grade is 34%, sulfur content is 1.2%, reduction temperature is 800°C, reduction time is 25min, drum type magnetic separator is selected three times (magnetic field strength 80 millitesla), and magnetite concentrate iron grade is obtained. 62.3%, iron recovery rate 81.3%, sulfur 0.48%, copper 0.11%, lead 0.019%, zinc 0.035%.
Embodiment 2
[0014] Embodiment 2: additive formula is (by weight): coal 70%, ferric chloride 15%, calcium carbonate 15%, sodium humate 5%. The dosage of additives is 5%, the iron grade of sulfuric acid slag is 34%, the sulfur content is 1.2%, the reduction temperature is 800°C, the reduction time is 20min, and the drum magnetic separator is separated three times (the magnetic field strength is 75 millitesla), and the iron grade of the magnetite concentrate is obtained. 62.0%, iron recovery rate 80.1%, sulfur 0.55%, copper 0.11%, lead 0.022%, zinc 0.033%.
Embodiment 3
[0015] Embodiment 3: additive formula is (by weight): coal 80%, iron trichloride 5%, calcium carbonate 5%, sodium humate 10%. Additive dosage is 3%, sulfuric acid slag iron grade is 34%, sulfur content is 1.2%, reduction temperature is 850°C, reduction time is 25min, drum type magnetic separator is selected three times (magnetic field strength 75 millitesla), and magnetite concentrate iron grade is obtained. 62.2%, iron recovery rate 80.8%, sulfur 0.50%, copper 0.13%, lead 0.020%, zinc 0.027%.
PUM
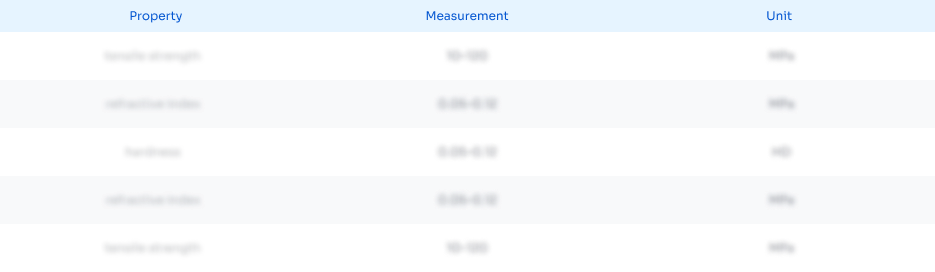
Abstract
Description
Claims
Application Information

- Generate Ideas
- Intellectual Property
- Life Sciences
- Materials
- Tech Scout
- Unparalleled Data Quality
- Higher Quality Content
- 60% Fewer Hallucinations
Browse by: Latest US Patents, China's latest patents, Technical Efficacy Thesaurus, Application Domain, Technology Topic, Popular Technical Reports.
© 2025 PatSnap. All rights reserved.Legal|Privacy policy|Modern Slavery Act Transparency Statement|Sitemap|About US| Contact US: help@patsnap.com