Device for preparing aluminum oxide self-efflorescence grog by fusion method and preparation method thereof
A technology of alumina and melting method, which is applied in the direction of alumina/hydroxide, etc., can solve the problems of high qualified rate of alumina clinker, and achieve the effects of saving energy consumption, simple operation, complete and rapid reaction
- Summary
- Abstract
- Description
- Claims
- Application Information
AI Technical Summary
Problems solved by technology
Method used
Image
Examples
Embodiment 1
[0034] Example 1: As shown in Figure 1, Figure 2, Figure 3, and Figure 4, the equipment for producing alumina self-powdering clinker by melting method includes a high-temperature fan 1, a hot air pipe 2, a calcining kiln 3, and a rotary distributor 4 , Elevator 5, cooler 6, dust collector 7, chimney 8, waste gas fan 9, feeding conveyor 11, waste gas pipe 12, communicate with cooler 6 and unloader 10. One end of the high-temperature fan 1 is connected to the secondary hot air pipe 13, the other end of the high-temperature fan 1 is connected to the hot air outlet of the hot air pipe 2 of the cooler, and the upper and lower ends of the secondary hot air pipe 13 are respectively connected to the calciner. 3 The upper and lower air chambers 14 and 15 of the outer wall, the feeding conveyor 11 is connected with the hoist 5, the hoist 5 is connected with the rotary distributor 4, and a feed inlet 17 is provided at the top of the calcining kiln 3, and the rotary distributor 4 is connec...
Embodiment 2
[0040] Embodiment 2: as shown in Figure 5, utilize the equipment of embodiment 1 to adopt the method for producing alumina self-powdering clinker prepared by melting method, comprising the following steps, (1), grinding process, (2), melting method The calcining process obtains the alumina clinker, and (3), the cooling process obtains the alumina self-powdering clinker;
[0041] Wherein (1), grinding process: with 20 tons of fly ash, 60 tons of limestone, carry out batching and grind;
[0042] (2) Alumina clinker obtained from the calcining process of the melting method: the raw material that is ground from step (1) is transported to the rotary distributor by the feeding conveyor through the hoist, and then enters from the feeding port at the top of the calcining kiln. calcining kiln;
[0043] (a) The materials entering the raw meal decomposition zone at the upper part of the calcining kiln are dried and dehydrated in the raw meal decomposition zone, and the reaction temperat...
Embodiment 3
[0049] Embodiment 3: as shown in Figure 5, utilize the equipment of embodiment 1 to adopt the method for producing alumina self-powdering clinker prepared by melting method, comprising the following steps, (1), grinding process, (2), melting method The calcining process obtains the alumina clinker, and (3), the cooling process obtains the alumina self-powdering clinker;
[0050] Wherein (1), grinding process: with 40 tons of fly ash, 80 tons of limestone, carry out batching and grind;
[0051] (2) Alumina clinker obtained from the calcining process of the melting method: the raw material that is ground from step (1) is transported to the rotary distributor by the feeding conveyor through the hoist, and then enters from the feeding port at the top of the calcining kiln. calcining kiln;
[0052] (a) The materials entering the raw meal decomposition zone at the upper part of the calciner are dried and dehydrated in the raw meal decomposition zone, and the reaction temperature in...
PUM
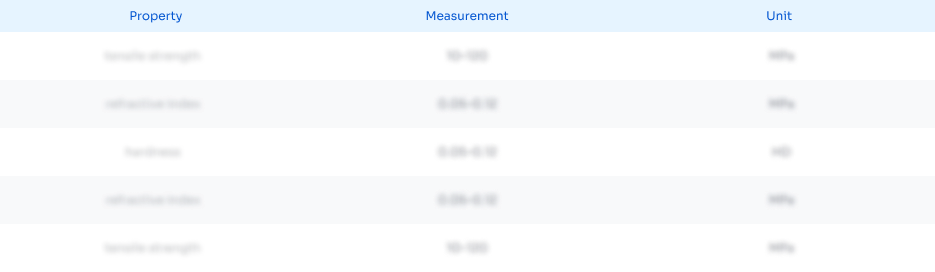
Abstract
Description
Claims
Application Information

- R&D Engineer
- R&D Manager
- IP Professional
- Industry Leading Data Capabilities
- Powerful AI technology
- Patent DNA Extraction
Browse by: Latest US Patents, China's latest patents, Technical Efficacy Thesaurus, Application Domain, Technology Topic, Popular Technical Reports.
© 2024 PatSnap. All rights reserved.Legal|Privacy policy|Modern Slavery Act Transparency Statement|Sitemap|About US| Contact US: help@patsnap.com