Pressure monitord by displacement type method for controlling fluid form machine for powder
A displacement monitoring and control method technology, which is applied in the direction of material forming presses, hydraulic controllers, presses, etc., can solve problems such as difficult control, brick pressure reduction, error, etc., to improve quality stability, facilitate installation and The effect of minor changes in maintenance and hardware structure
- Summary
- Abstract
- Description
- Claims
- Application Information
AI Technical Summary
Problems solved by technology
Method used
Image
Examples
Embodiment Construction
[0009] Fig. 1 is a working principle diagram of the present invention applied to a moving beam ceramic tile press. The moving beam ceramic tile press includes a workbench 1 fixed to a frame, and a moving beam 2 that can move up and down. The moving beam 2 is actually a piston cylinder that can move up and down. When hydraulic oil is injected into the cylinder, the moving beam 2 moves downward. The pressure of the downward movement of the moving beam 2 to press the powder is controlled by the closed-loop hydraulic control system. The upper and lower molds 3 and 4 are installed on the moving beam 2 and the workbench 1 respectively. In order to measure the relative displacement of the molds 3 and 4, a grating digital displacement sensor 5 is installed between the moving beam 2 and the workbench 1. The fixed grating ruler 5b in the sensor is fixed on the frame, and the moving grating ruler 5a follows the beam 2 exercise together. The ceramic powder 6 to be pressed is filled and...
PUM
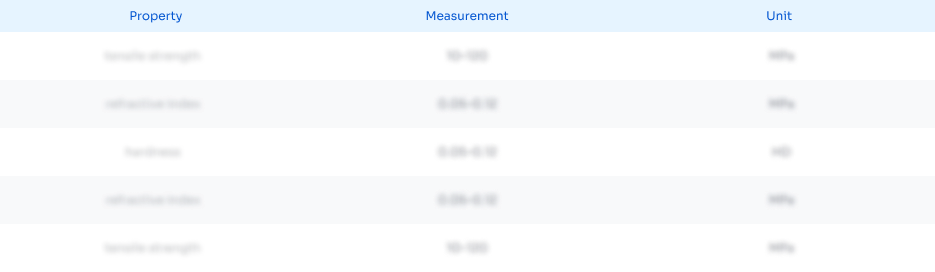
Abstract
Description
Claims
Application Information

- Generate Ideas
- Intellectual Property
- Life Sciences
- Materials
- Tech Scout
- Unparalleled Data Quality
- Higher Quality Content
- 60% Fewer Hallucinations
Browse by: Latest US Patents, China's latest patents, Technical Efficacy Thesaurus, Application Domain, Technology Topic, Popular Technical Reports.
© 2025 PatSnap. All rights reserved.Legal|Privacy policy|Modern Slavery Act Transparency Statement|Sitemap|About US| Contact US: help@patsnap.com