Production method of silicomangan of sintering powder by rotary kiln and hot filling in ore-smelting electric furnace
A submerged thermal electric furnace, silicon-manganese alloy technology, which is applied in other directions such as non-combustion heat generation and heating devices, can solve the problems of inability to utilize waste heat, less pollution to the environment, and less pollution to the environment, so as to save electricity consumption and pollute the environment. , the effect of reducing the greenhouse effect
- Summary
- Abstract
- Description
- Claims
- Application Information
AI Technical Summary
Problems solved by technology
Method used
Image
Examples
Embodiment 1
[0016] As shown in the accompanying drawings, the silicon-manganese alloy production method using the rotary kiln sintering powder and hot charging submerged thermal electric furnace in the present embodiment comprises the following steps:
[0017] a. Ingredients: First, crush silica, manganese ore, dolomite, manganese-rich slag and high-iron manganese ore into powders with a particle size of less than 50mm and put them into the receiving bin respectively. The amount of manganese is different, calculate the ratio of raw materials, carry out batching and mix evenly;
[0018] b. Sintering powder: The mixed powder is metered into the kiln tail of the rotary kiln, sintered into a material with a particle size of 5-70 mm in the sintering zone of the rotary kiln, and discharged from the kiln head of the rotary kiln. The temperature in the sintering zone of the rotary kiln is 850 ℃-1300℃, the time of the material in the rotary kiln is 50 minutes;
[0019] c. Hot-charging submerged t...
Embodiment 2
[0025] As shown in the accompanying drawings, the silicon-manganese alloy production method using the rotary kiln sintering powder and hot charging submerged thermal electric furnace in the present embodiment comprises the following steps:
[0026] a. Ingredients: First, crush silica, manganese ore, dolomite, manganese-rich slag and high-iron manganese ore into powders with a particle size of less than 50mm and put them into the receiving bin respectively. The amount of manganese is different, calculate the ratio of raw materials, carry out batching and mix evenly;
[0027] b. Sintering powder: The mixed powder is metered into the kiln tail of the rotary kiln, sintered into a material with a particle size of 5-70 mm in the sintering zone of the rotary kiln, and discharged from the kiln head of the rotary kiln. The temperature in the sintering zone of the rotary kiln is 850 ℃-1300℃, the time of the material in the rotary kiln is 60 minutes;
[0028] c. Hot-charging submerged t...
Embodiment 3
[0034] As shown in the accompanying drawings, the silicon-manganese alloy production method using the rotary kiln sintering powder and hot charging submerged thermal electric furnace in the present embodiment comprises the following steps:
[0035] a. Ingredients: First, crush silica, manganese ore, dolomite, manganese-rich slag and high-iron manganese ore into powders with a particle size of less than 50mm and put them into the receiving bin respectively. The amount of manganese is different, calculate the ratio of raw materials, carry out batching and mix evenly;
[0036] b. Sintering powder: The mixed powder is metered into the kiln tail of the rotary kiln, sintered into a material with a particle size of 5-70 mm in the sintering zone of the rotary kiln, and discharged from the kiln head of the rotary kiln. The temperature in the sintering zone of the rotary kiln is 850 ℃-1300℃, the time of the material in the rotary kiln is 70 minutes;
[0037] c. Hot-charging submerged t...
PUM
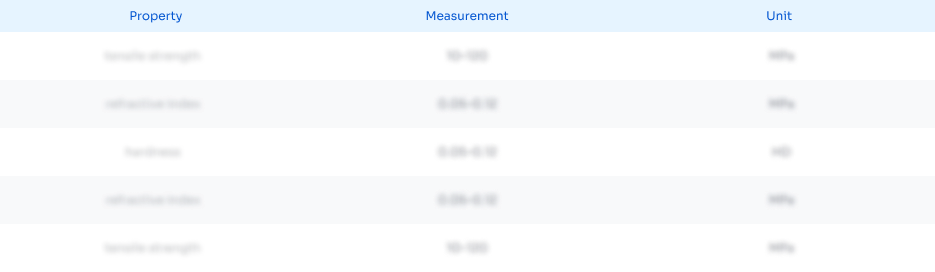
Abstract
Description
Claims
Application Information

- R&D
- Intellectual Property
- Life Sciences
- Materials
- Tech Scout
- Unparalleled Data Quality
- Higher Quality Content
- 60% Fewer Hallucinations
Browse by: Latest US Patents, China's latest patents, Technical Efficacy Thesaurus, Application Domain, Technology Topic, Popular Technical Reports.
© 2025 PatSnap. All rights reserved.Legal|Privacy policy|Modern Slavery Act Transparency Statement|Sitemap|About US| Contact US: help@patsnap.com