Photoetching patterning method with micro-transfer patterned graph as mask plate
A photolithographic patterning and patterning technology, which is applied in the direction of photoplate making process, optics, and optomechanical equipment on the patterned surface, can solve the problems of low patterning accuracy and complicated processing process
- Summary
- Abstract
- Description
- Claims
- Application Information
AI Technical Summary
Problems solved by technology
Method used
Image
Examples
Embodiment 1
[0021] (1) Deposit a gold film 4 on the surface of the patterned polydimethylsiloxane soft stamp 5 .
[0022] (2) Coating a photoresist film 2 on the silicon wafer 1, after drying the photoresist film 2, coating a layer of polystyrene film 3 on the surface of the photoresist film 2 and drying.
[0023] (3) Fit the polydimethylsiloxane soft stamp 5 with the gold film 4 deposited on the surface to the surface of the polystyrene film 3, heat the whole system to 100° C., and keep it for 5 minutes. Then the temperature of the whole system was lowered to 20° C., and the polydimethylsiloxane soft stamp 5 was peeled off to obtain a polystyrene film 3 with a gold film pattern 6 on the surface.
[0024] (4) The polystyrene film 3 with the gold film pattern 6 in step (3) is carried out oxygen-reactive ion etching, and the polystyrene film 3 without the gold film pattern 6 on the surface is etched and removed to obtain a polystyrene film Pattern 7.
Embodiment 2
[0027] (1) Deposit a gold film 4 on the surface of the patterned polydimethylsiloxane soft stamp 5 .
[0028] (2) Coating a photoresist film 2 on the ITO glass 1, after drying the photoresist film 2, coating a layer of polystyrene film 3 on the surface of the photoresist film 2 and drying.
[0029] (3) Fit the polydimethylsiloxane soft stamp 5 with the gold film 4 deposited on the surface to the surface of the polystyrene film 3, heat the whole system to 110° C., and keep it for 3 minutes. Then the temperature of the whole system was lowered to 30° C., and the polydimethylsiloxane soft stamp 5 was peeled off to obtain a polystyrene film 3 with a gold film pattern 6 on the surface.
[0030] (4) The polystyrene film 3 with the gold film pattern 6 in step (3) is electrodeposited a layer of metal copper in copper sulfate solution, then the polystyrene film 3 with the gold film pattern 6 that has been electrodeposited copper Oxygen reactive ion etching is carried out, and the poly...
Embodiment 3
[0033] (1) Deposit a gold film 4 on the surface of the patterned polydimethylsiloxane soft stamp 5 .
[0034] (2) Coating a photoresist film 2 on the glass 1, after drying the photoresist film 2, coating a layer of polystyrene film 3 on the surface of the photoresist film 2 and drying.
[0035] (3) Fit the polydimethylsiloxane soft stamp 5 with the gold film 4 deposited on the surface to the surface of the polystyrene film 3, heat the whole system to 120° C., and keep it for 1 minute. Then the temperature of the whole system was lowered to 50° C., and the polydimethylsiloxane soft stamp 5 was peeled off to obtain a polystyrene film 3 with a gold film pattern 6 on the surface.
[0036] (4) The polystyrene film 3 with the gold film pattern 6 in step (3) is carried out oxygen-reactive ion etching, and the polystyrene film 3 without the gold film pattern 6 on the surface is etched and removed to obtain a polystyrene film Pattern 7.
[0037] (5) The glass 1 treated in step (4) is...
PUM
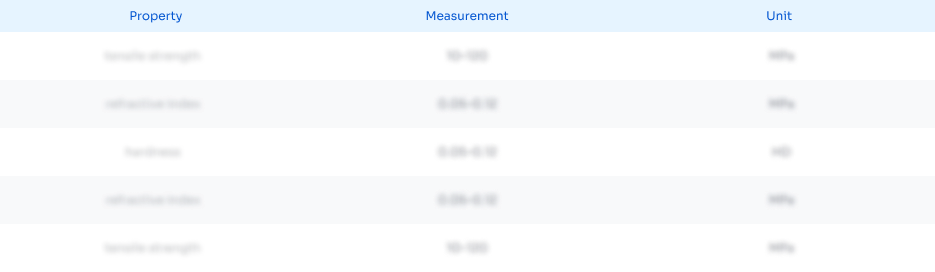
Abstract
Description
Claims
Application Information

- R&D
- Intellectual Property
- Life Sciences
- Materials
- Tech Scout
- Unparalleled Data Quality
- Higher Quality Content
- 60% Fewer Hallucinations
Browse by: Latest US Patents, China's latest patents, Technical Efficacy Thesaurus, Application Domain, Technology Topic, Popular Technical Reports.
© 2025 PatSnap. All rights reserved.Legal|Privacy policy|Modern Slavery Act Transparency Statement|Sitemap|About US| Contact US: help@patsnap.com