Composite calcium-base lubricating grease and its prepn
A technology of composite calcium base and lubricating grease, which is applied in the direction of lubricating compositions, petroleum industry, additives, etc., can solve the problems of complex production raw materials and processes, and achieve the effects of small change in surface hardening value, good oxidation stability, and easy operation
- Summary
- Abstract
- Description
- Claims
- Application Information
AI Technical Summary
Problems solved by technology
Method used
Image
Examples
Embodiment 1
[0051] In this example, the first method is used to prepare complex calcium-based grease.
[0052] At room temperature, take 630g of 500SN with a viscosity of 15cSt at 100°C, 1000ml of absolute ethanol and 120g of tetrabutyl titanate into the fat-making kettle, stir for 2 hours, add 62g of 12-hydroxystearic acid, and stir at 50°C for 4 hours. Thereafter, add 8.1 g of glacial acetic acid and 1.94 g of n-octanoic acid, stir evenly, then add 40.8 g of calcium hydroxide suspension with a concentration of 16.6% by weight, stir, continue to heat up to 220° C., and add 320 g of quenching oil. When the temperature drops below 70°C, take out the kettle. Grind twice with a three-wheel mill. The composition and properties of the product are shown in Table 1. The content of each component in the lubricating grease is 89.9% of base oil, 7.5% of thickener and 2.6% of titanium dioxide.
Embodiment 2
[0054] In this example, the second method is used to prepare complex calcium-based grease.
[0055] Add 47g of titanium tetrachloride to a beaker containing 100g of benzene under uniform stirring, slowly add 427g of isopropanol, and add 5mol / L ammonia water until the pH value is 6.5. After the reaction stopped, the reaction product was left to stand for 10 hours and then filtered, the ammonium chloride precipitate was separated from the titanium isopropoxide, and the filtrate titanium alkoxide was hydrolyzed with boiling water, and vigorously stirred to form a gel. Put it in a grease kettle.
[0056] Add 600g of ester oil with a viscosity of 20cSt at 100°C to this kettle, add 728g of calcium hydroxide suspension with a concentration of 12.5% by weight, and after rapid stirring, add 118.28g of benzoic acid and 28.29g of boric acid, and add at 88°C 12-Hydroxystearic acid 98.18g, thereafter the temperature was gradually raised to 240°C, and 250g of quenching oil was added. Wh...
Embodiment 3
[0058] In this example, the first method is used to prepare complex calcium-based grease.
[0059] At room temperature, take 500g of 500SN with a viscosity of 15cSt at 100°C, 800ml of acetone, and 118g of tetrabutyl titanate into the fat-making kettle. After stirring for 3 hours, add 66g of 12-hydroxystearic acid. After stirring at 60°C for 6 hours, add ice Acetic acid 66g, adding concentration is 326g of calcium hydroxide solution of 15% by weight, gradually heating up to 220 ℃, adding 270g of quenching oil. When the temperature drops below 70°C, take out the kettle. Grind twice with a three-wheel mill. The content of each component in the lubricating grease is 18.4% of thickener, 78.6% of base oil and 3.0% of titanium dioxide. The composition and properties of the product are shown in Table 1.
PUM
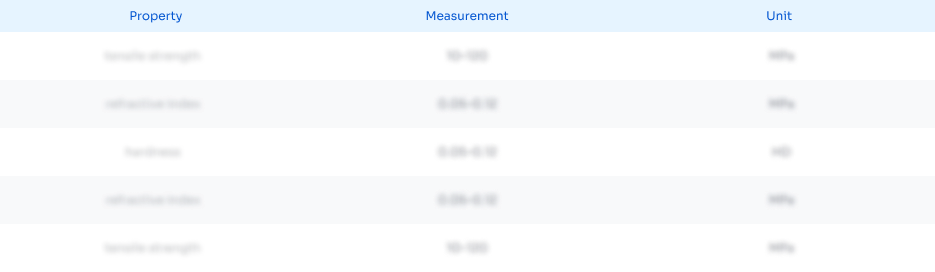
Abstract
Description
Claims
Application Information

- R&D
- Intellectual Property
- Life Sciences
- Materials
- Tech Scout
- Unparalleled Data Quality
- Higher Quality Content
- 60% Fewer Hallucinations
Browse by: Latest US Patents, China's latest patents, Technical Efficacy Thesaurus, Application Domain, Technology Topic, Popular Technical Reports.
© 2025 PatSnap. All rights reserved.Legal|Privacy policy|Modern Slavery Act Transparency Statement|Sitemap|About US| Contact US: help@patsnap.com