Process for preparing Cu-Zn-Al vapor hydroformylation catalyst and products therefrom
A hydrogenation catalyst, copper-zinc-aluminum technology, applied in chemical instruments and methods, metal/metal oxide/metal hydroxide catalysts, physical/chemical process catalysts, etc., can solve the problem of poor selectivity and stability, and low mechanical strength , poor product selectivity and other problems, to achieve the effect of inhibiting esterification and etherification side reactions, improving crystallization state, and improving selectivity
- Summary
- Abstract
- Description
- Claims
- Application Information
AI Technical Summary
Problems solved by technology
Method used
Examples
Embodiment 1
[0029] Catalyst preparation method of the present invention is as follows:
[0030] 117g copper nitrate and 171g zinc nitrate are made into 1200ml of copper and zinc mixed solution; Sodium solution, and flow into a neutralization tank with heat preservation and stirring for neutralization and aging, control the neutralization temperature at about 80°C, adjust the pH value to 7.0-8.0 through sodium carbonate solution, and then mix the copper and zinc mixed solution with 100% by weight The sodium carbonate solution with a content of 15.7% was added to the same neutralization tank concurrently, neutralized and aged under stirring, washed four times with deionized water at 40-50°C, and after drying the obtained filter cake, put it at 360 Calcined at ~400°C for 4-5 hours, and then added 2% of the total mass of the obtained material into graphite pellets to form catalyst sample 1.
[0031] In the product, copper oxide is 38.3%, zinc oxide is 58.1%, aluminum oxide is 1.6%, graphite ...
Embodiment 2
[0033] 117g copper nitrate and 202g zinc nitrate are made into 1200ml of copper and zinc mixed solution; The sodium solution is added into a neutralization tank with heat preservation and stirring for neutralization and aging, and the neutralization temperature is controlled at about 80°C, and the pH value is 7.0 to 8.0, and then the mixed solution of copper and zinc is mixed with 15.7% by weight of carbonic acid Add the sodium solution into the same neutralization tank in parallel, neutralize and age under stirring, wash four times with deionized water at 40-50°C, dry the obtained filter cake, and roast at 360-400°C for 4- After 5 hours, 2% of the total mass of the obtained material was added into a graphite tablet to form a catalyst sample 2.
[0034] In the product, copper oxide is 34.2%, zinc oxide is 62.3%, and aluminum oxide is 1.4%.
Embodiment 3
[0036] 117g copper nitrate and 218g zinc nitrate are made into 1200ml of copper and zinc mixed solution; The sodium solution is added into a neutralization tank with heat preservation and stirring for neutralization and aging, and the neutralization temperature is controlled at about 80°C, and the pH value is 7.0 to 8.0, and then the mixed solution of copper and zinc is mixed with 15.7% by weight of carbonic acid Add the sodium solution into the same neutralization tank in parallel, neutralize and age under stirring, wash four times with deionized water at 40-50°C, dry the obtained filter cake, and roast at 360-400°C for 4- After 5 hours, 2% of the total mass of the obtained material was added to form a graphite tablet to obtain catalyst sample 3. The neutralization reaction includes primary neutralization reaction and second neutralization reaction.
[0037] In the product, copper oxide is 31.8%, zinc oxide is 64.1%, and aluminum oxide is 2.1%.
PUM
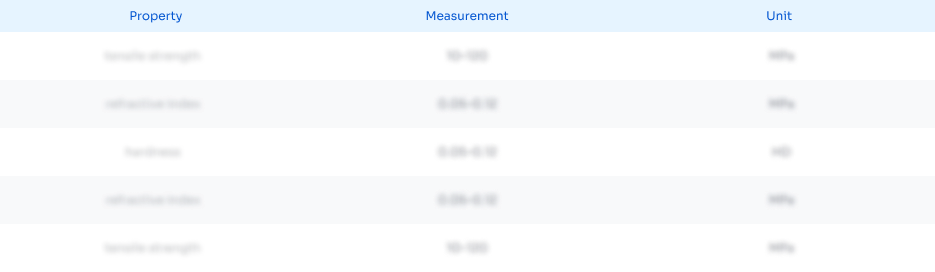
Abstract
Description
Claims
Application Information

- Generate Ideas
- Intellectual Property
- Life Sciences
- Materials
- Tech Scout
- Unparalleled Data Quality
- Higher Quality Content
- 60% Fewer Hallucinations
Browse by: Latest US Patents, China's latest patents, Technical Efficacy Thesaurus, Application Domain, Technology Topic, Popular Technical Reports.
© 2025 PatSnap. All rights reserved.Legal|Privacy policy|Modern Slavery Act Transparency Statement|Sitemap|About US| Contact US: help@patsnap.com