Method for preparing high temperature resistant phenol-formaldehyde foam composite thermal-insulating materials
A composite thermal insulation material and phenolic foam technology, which is applied in the field of preparation of high temperature-resistant phenolic foam composite thermal insulation materials, can solve problems such as unsafe thermal insulation building materials, achieve high thermal insulation effect, excellent thermal insulation performance, and improve the effect of heat resistance grade.
- Summary
- Abstract
- Description
- Claims
- Application Information
AI Technical Summary
Problems solved by technology
Method used
Image
Examples
Embodiment 1
[0038] Add 4500g resole phenolic resin, 180g sorbitan oleate polyoxyethylene ether, trade name Tween-80, 22g boron trioxide, 1000g aluminum hydroxide, 400g pentane and 630g mixed acid curing agent into the mixing pot in sequence , stir at high speed for 15 seconds, quickly and evenly pour 100 to pay 0.06m 3 In the plate mold or pipe mold, lay a 3mm thick glass fiber felt, close the mold, foam and solidify at 60°C for 1 hour, cool, demould, and the density is 100kg / m 3 Left and right high temperature resistant phenolic foam composite insulation materials.
Embodiment 2
[0040] Add 4500g resole phenolic resin, 75g Tween-80, 60g boron powder, 3000g aluminum hydroxide, 650g pentane and 400g mixed acid curing agent into the mixing pot in turn, stir at high speed for 40 seconds, quickly and evenly pour 250 to 0.06m 3 In the plate mold or pipe mold, spread 10mm thick ceramic fiber felt, close the mold, foam and solidify at 85°C for 45min, cool, demould, and the density is 50kg / m 3 Left and right high temperature resistant phenolic foam composite insulation materials.
Embodiment 3
[0042] Add 4500g resole phenolic resin, 350g Tween-80, 450g zinc borate, 1500g aluminum hydroxide, 500g pentane and 600g mixed acid curing agent into the mixing pot in turn, stir at high speed for 15 seconds, quickly and evenly pour 200 to 0.06m 3In the plate mold or pipe mold, lay 6mm thick mineral wool felt, close the mold, foam and solidify at 70°C for 1.5 hours, cool, demould, and the density is 40kg / m 3 Left and right high temperature resistant phenolic foam composite insulation materials.
PUM
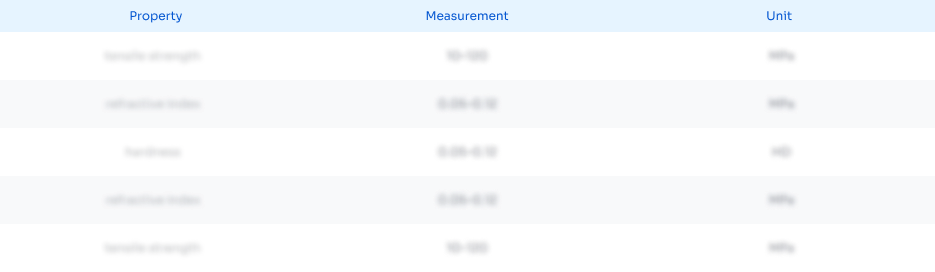
Abstract
Description
Claims
Application Information

- Generate Ideas
- Intellectual Property
- Life Sciences
- Materials
- Tech Scout
- Unparalleled Data Quality
- Higher Quality Content
- 60% Fewer Hallucinations
Browse by: Latest US Patents, China's latest patents, Technical Efficacy Thesaurus, Application Domain, Technology Topic, Popular Technical Reports.
© 2025 PatSnap. All rights reserved.Legal|Privacy policy|Modern Slavery Act Transparency Statement|Sitemap|About US| Contact US: help@patsnap.com