Boron contg. multi-element low alloyed wearable cast steel and prepn. thereof
A low-alloy, multi-component technology, applied in the field of wear-resistant metal materials, can solve the problems of increasing production costs, achieve the effect of improving strength and wear resistance, improving mechanical properties, and simple heat treatment process
- Summary
- Abstract
- Description
- Claims
- Application Information
AI Technical Summary
Problems solved by technology
Method used
Examples
Embodiment 1
[0036] The boron-containing multi-element low-alloy wear-resistant cast steel of this embodiment is smelted in a 500kg intermediate frequency induction electric furnace. First, use scrap steel, ferrosilicon, ferrochromium, and ferromanganese as ingredients, add carbon with pig iron, melt molten steel, adjust the composition before the furnace, and raise the temperature to 1630 ℃, add silicon-calcium alloy, ferroboron, ferro-titanium and containing Nitrochromium iron is then released. The yttrium-based rare earth magnesium alloy and potassium-containing material are crushed into small pieces with a particle size of less than 15mm, dried at 160°C, and placed at the bottom of the ladle, and the molten steel is compositely modified by the ladle flushing method. After the modification treatment, the molten steel is poured into a casting, and the molten steel pouring temperature is 1490°C. After the casting is austenitized at 960℃×1h, it is rapidly cooled, and then kept at 280℃ for 2.5h...
Embodiment 2
[0040] The boron-containing multi-element low-alloy wear-resistant cast steel of this embodiment is smelted in a 1500kg electric arc furnace. First, use scrap steel, ferrosilicon, ferrochrome, and ferromanganese as ingredients, use waste graphite electrodes to increase carbon, melt the molten steel, adjust the composition before the furnace, and raise the temperature to 1655°C. Add silicon-calcium alloy, ferro-boron, and ferro-titanium before the furnace is discharged And nitrogen-containing ferrochromium, and then baked. The yttrium-based rare earth magnesium alloy and potassium-containing material are crushed into small pieces with a particle size of less than 15mm, dried at 150°C, placed at the bottom of the ladle, and the molten steel is compositely modified by the ladle flushing method. After the modification treatment, the molten steel is poured into a casting, and the molten steel pouring temperature is 1508℃. After the casting is austenitized at 880℃×3.5h, it is rapidly co...
PUM
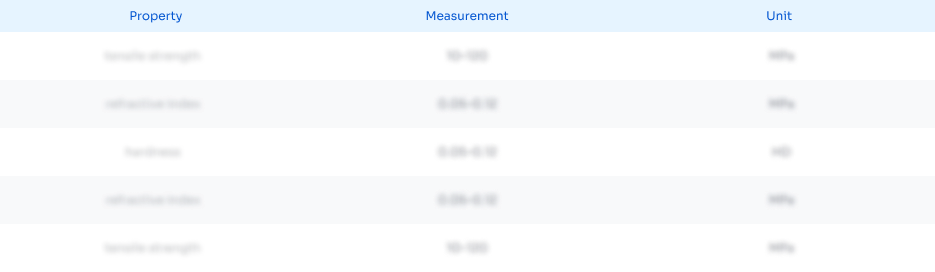
Abstract
Description
Claims
Application Information

- R&D
- Intellectual Property
- Life Sciences
- Materials
- Tech Scout
- Unparalleled Data Quality
- Higher Quality Content
- 60% Fewer Hallucinations
Browse by: Latest US Patents, China's latest patents, Technical Efficacy Thesaurus, Application Domain, Technology Topic, Popular Technical Reports.
© 2025 PatSnap. All rights reserved.Legal|Privacy policy|Modern Slavery Act Transparency Statement|Sitemap|About US| Contact US: help@patsnap.com