Composite yarn manufacturing method
A manufacturing method and yarn technology, which is applied in the field of manufacturing new composite yarns, can solve problems such as high process requirements, products that cannot meet market requirements, and complicated processes, and achieve soft and comfortable hand feeling, good chemical resistance and dyeing performance, The effect of reducing environmental pollution
- Summary
- Abstract
- Description
- Claims
- Application Information
AI Technical Summary
Problems solved by technology
Method used
Examples
Embodiment 1
[0042] A new type of composite yarn, the composite yarn is made of viscose fiber and polytrimethylene terephthalate fiber on a twisting machine or a covering yarn machine, twisted and plyed to make a white yarn, and then passed through It is made by pre-treatment, dyeing, washing, softening and finishing. The poly(trimethylene terephthalate) fiber refers to a compound polyester fiber obtained by esterification and polycondensation of terephthalic acid and 1,3-propanediol.
[0043] A kind of manufacture method of novel composite yarn is realized by following steps:
[0044] a: Twisting and plying; twisting and plying viscose filaments and polytrimethylene terephthalate fibers on a twisting machine or a covered yarn machine to make white blank yarn;
[0045] b: Pre-treatment, immerse the white blank yarn made in step a above into soft water at normal temperature, and add 0.5 g / L of cleaning agent and 1 g / L of soda ash according to the volume of soft water in the soft water at n...
Embodiment 2
[0053]A new type of composite yarn, the composite yarn is made of viscose fiber and polytrimethylene terephthalate fiber on a twisting machine or a covering yarn machine, twisted and plyed to make a white yarn, and then passed through It is made by pre-treatment, dyeing, washing, softening and finishing. The poly(trimethylene terephthalate) fiber refers to a compound polyester fiber obtained by esterification and polycondensation of terephthalic acid and 1,3-propanediol.
[0054] A kind of manufacture method of novel composite yarn is realized by following steps:
[0055] a: Twisting and plying; twisting and plying viscose filaments and polytrimethylene terephthalate fibers on a twisting machine or a covered yarn machine to make white blank yarn;
[0056] b: Pretreatment, immerse the blank yarn made in step a above into soft water at room temperature, and add detergent 1g / L and soda ash 2g / L in soft water at room temperature according to the volume of soft water, and then hea...
Embodiment 3
[0063] A new type of composite yarn, the composite yarn is made of viscose fiber and polytrimethylene terephthalate fiber on a twisting machine or a covering yarn machine, twisted and plyed to make a white yarn, and then passed through It is made by pre-treatment, dyeing, washing, softening and finishing. The poly(trimethylene terephthalate) fiber refers to a compound polyester fiber obtained by esterification and polycondensation of terephthalic acid and 1,3-propanediol.
[0064] A kind of manufacture method of novel composite yarn is realized by following steps:
[0065] a: Twisting and plying; twisting and plying viscose filaments and polytrimethylene terephthalate fibers on a twisting machine or a covered yarn machine to make white blank yarn;
[0066] b: pretreatment, immerse the white blank yarn made in the above step a into soft water at normal temperature, and add 0.7g / L of cleaning agent and 1.5g / L of soda ash according to the volume of soft water in the soft water a...
PUM
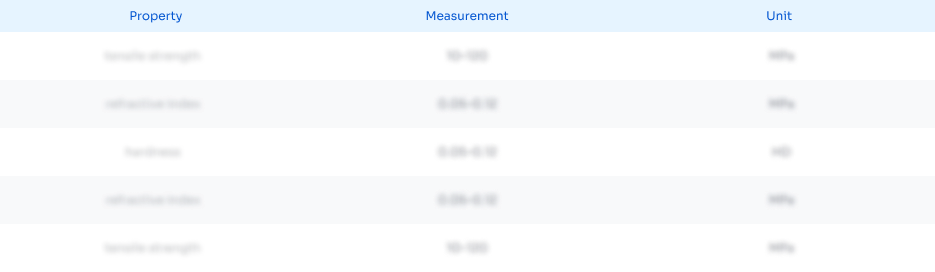
Abstract
Description
Claims
Application Information

- R&D Engineer
- R&D Manager
- IP Professional
- Industry Leading Data Capabilities
- Powerful AI technology
- Patent DNA Extraction
Browse by: Latest US Patents, China's latest patents, Technical Efficacy Thesaurus, Application Domain, Technology Topic, Popular Technical Reports.
© 2024 PatSnap. All rights reserved.Legal|Privacy policy|Modern Slavery Act Transparency Statement|Sitemap|About US| Contact US: help@patsnap.com