Canapina-fiber regenerated fiber and ramie-fiber union shell fabric and producing method
A technology of regenerated fiber and ramie fiber, which is applied in textiles, textiles, papermaking, fabrics, etc., and can solve the problems of pure ramie products such as difficulty in weaving, itchy wearing performance, and high cost
- Summary
- Abstract
- Description
- Claims
- Application Information
AI Technical Summary
Problems solved by technology
Method used
Examples
Embodiment 1
[0015] make 21 s ×21 s ×52×58×63 fabric.
[0016] Choose hemp regenerated fiber and ramie fiber (short fiber), the ratio is 55:45, and they are evenly stacked in the plucking machine, and after grabbing, mixing, opening, and removing impurities, they are rolled into rolls, and the weight of the rolls is controlled at 450. ±5 g / m; the roll is carded into slivers, the speed of the carding licker-in is controlled at 850-900 rpm (900 rpm in this embodiment), the draft ratio is 107 times, and the carding sliver weighs 22.5 g / min 5 meters; the sliver after carding is further evenly straightened on the drawing frame and combined into mature sliver, and the drawing draft ratio is controlled at 7.5-8.5 times (the present embodiment is 8 times), and the drawing process conditions are as follows: roller gauge : 9×12(mm), front roller speed: 2000 rpm.
[0017] Spinning is that cooked sliver is spun into roving, and the spinning roving process condition is that the draft ratio of roving...
Embodiment 2
[0024] make 28 s ×28 s ×59×62×63 new ramie fabric.
[0025] Select hemp regenerated fiber strips and ramie fiber strips (medium-length fibers), the ratio of which is 90:10, mix the hemp regenerated fiber strips and ramie strips on the needle carding machine, and evenly draft the mature strips, and control the drafting ratio of the needle combs In 7.5-9.5 times (the present embodiment is 8 times). The technological conditions are needle plate striking times: 852 times / minute, needle plate specification: 7-13 needles / hour, back tension: 1.013, front tension: 1.014.
[0026] Spinning is that cooked sliver is spun into roving, and the process condition of spinning head roving is that the draft ratio of roving is controlled at 6.5-8.5 times (the present embodiment is 8.5 times), spindle speed: 300 rpm, front roller speed: 185 rpm / min, the twist coefficient is 19; the process condition of spinning the second roving is that the draft ratio of the roving is controlled at 6.5-8.5 t...
Embodiment 3
[0032] make 10 s ×10 s ×72×50×63 Herringbone denim fabric
[0033] Choose hemp regenerated fiber and ramie fiber (short fiber), the ratio is 40:60, and they are evenly stacked in the plucking machine. After grabbing, mixing, opening, and removing impurities, they are rolled into rolls, and the weight of the rolls is controlled at 450. ±5 g / m; the roll is carded into strips, the speed of the carding licker-in is controlled at 850-900 rpm (900 rpm in this embodiment), the draft ratio is 107 times, and the carding sliver weighs 22.5g / min. 5 meters; the sliver after carding is further evenly straightened on the drawing frame and combined into mature sliver, and the drawing draft ratio is controlled at 7.5-8.5 times (the present embodiment is 8 times), and the drawing process conditions are as follows: roller gauge : 9×12(mm), front roller speed: 2000 rpm.
[0034] Spinning is that cooked sliver is made into yarn through air spinning, and its process conditions are: opening roll...
PUM
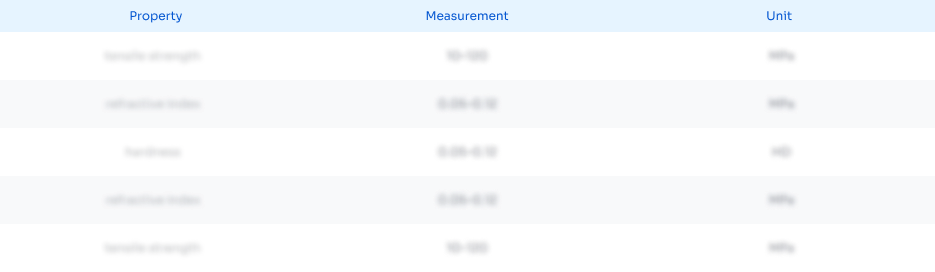
Abstract
Description
Claims
Application Information

- R&D
- Intellectual Property
- Life Sciences
- Materials
- Tech Scout
- Unparalleled Data Quality
- Higher Quality Content
- 60% Fewer Hallucinations
Browse by: Latest US Patents, China's latest patents, Technical Efficacy Thesaurus, Application Domain, Technology Topic, Popular Technical Reports.
© 2025 PatSnap. All rights reserved.Legal|Privacy policy|Modern Slavery Act Transparency Statement|Sitemap|About US| Contact US: help@patsnap.com