Method for preparing middle ladle dry vabrative material
A vibrating material and vibrating forming technology, applied in the field of preparation of dry vibrating material in tundish, can solve the problems of carbon increase, environmental pollution, irritation, etc., and achieve the effects of good corrosion resistance, environmental friendliness and easy disassembly
- Summary
- Abstract
- Description
- Claims
- Application Information
AI Technical Summary
Problems solved by technology
Method used
Examples
Embodiment Construction
[0008] [Example] 1 A preparation method of tundish dry vibration material for 28 tons of continuous casting
[0009] In weight percentage: 90% of sintered magnesia containing 97% of MgO, 10% of sodium metasilicate. Wherein the weight percentage of the gradation of the sintered magnesia is: 80-85% for 1-0.088mm, and 15-20% for <0.088mm. The above-mentioned raw materials are mixed, stirred evenly, molded by tire membrane vibration, baked at 110-300°C, and demolded to obtain the tundish lining.
[0010] Its measured index: MgO is 89.4%, SiO 2 6.2%; bulk density: 110℃×24h 2.18g / cm 3 ; Compressive strength: 110℃×24h3.6MPa, 7.3MPa after burning at 1500℃×3h; linear change rate: -1.2% after burning at 1500℃×3h. This material is used in 28-ton continuous casting tundish, and its service life can reach more than 26 furnaces.
[0011] The characteristics of this embodiment are: ①Easy construction; ②Quick baking without bursting or peeling, short baking time, and no smell; ③Good corro...
PUM
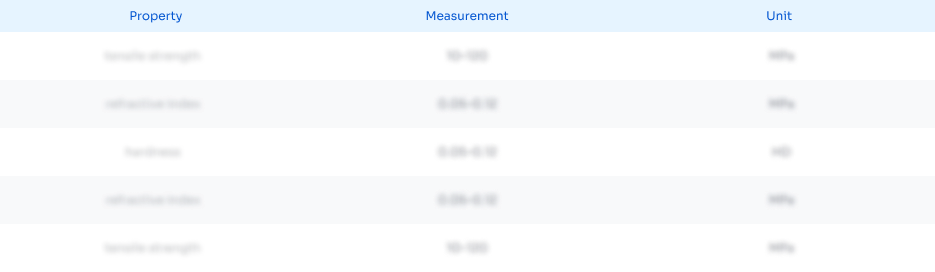
Abstract
Description
Claims
Application Information

- R&D Engineer
- R&D Manager
- IP Professional
- Industry Leading Data Capabilities
- Powerful AI technology
- Patent DNA Extraction
Browse by: Latest US Patents, China's latest patents, Technical Efficacy Thesaurus, Application Domain, Technology Topic, Popular Technical Reports.
© 2024 PatSnap. All rights reserved.Legal|Privacy policy|Modern Slavery Act Transparency Statement|Sitemap|About US| Contact US: help@patsnap.com