Method for preparing erosion-wear-resisting composite coating
A composite coating, erosion-resistant technology, used in coatings, metal material coating processes, manufacturing tools, etc., can solve problems such as spalling, power station boiler pipe protection, burst pipe leakage, etc., to extend service life and operate safely. Guaranteed effect
- Summary
- Abstract
- Description
- Claims
- Application Information
AI Technical Summary
Problems solved by technology
Method used
Image
Examples
Embodiment 1
[0016] Firstly, the metal substrate is cleaned to remove rust, dirt, etc. on the surface, and then a layer of hard alloy spots is spot-welded on the cleaned and decontaminated metal substrate with a self-developed self-protecting metal core spot surfacing welding wire. array. The welding current is 180-220A, the welding voltage is 18-22V, the distance between solder joints is 2mm, the diameter of solder joints is 4mm, and the height of solder joints is 2mm. The Rockwell hardness of the solder joint is HRC51. The metal substrate after spot surfacing is sandblasted and roughened, and a layer of erosion-resistant and wear-resistant coating is sprayed on the metal substrate after sandblasting and roughened by the prior art. The spraying current is 150-180A, the spraying voltage is 30-32V, and the spraying Air pressure 0.55MP, spraying distance 150mm. The thickness of the sprayed layer is 5mm, and the Rockwell hardness of the surface of the sprayed layer is about 60 (HR45N). The...
Embodiment 2
[0018] Firstly, the metal substrate is cleaned to remove rust, dirt, etc. on the surface, and then a layer of hard alloy spots is spot-welded on the cleaned and decontaminated metal substrate with a self-developed self-protecting metal core spot surfacing welding wire. array. The welding current is 180-220A, the welding voltage is 18-22V, the distance between solder joints is 3mm, the diameter of solder joints is 4mm, and the height of solder joints is 3mm. The Rockwell hardness of the solder joint is HRC50. The metal substrate after spot surfacing is sandblasted and roughened, and a layer of erosion-resistant and wear-resistant coating is sprayed on the metal substrate after sandblasting and roughened by the prior art. The spraying current is 150-180A, the spraying voltage is 30-32V, and the spraying Air pressure 0.55MP, spraying distance 150mm. The thickness of the sprayed layer is 8mm, and the Rockwell hardness of the surface of the sprayed layer is about 62 (HR45N). The...
Embodiment 3
[0020] Firstly, the metal substrate is cleaned to remove rust, dirt, etc. on the surface, and then a layer of hard alloy spots is spot-welded on the cleaned and decontaminated metal substrate with a self-developed self-protecting metal core spot surfacing welding wire. Array. The welding current is 180-220A, the welding voltage is 18-22V, the distance between solder joints is 4mm, the diameter of solder joints is 5mm, and the height of solder joints is 2mm. The Rockwell hardness of the solder joint is HRC52. The metal substrate after spot surfacing is sandblasted and roughened, and a layer of erosion-resistant and wear-resistant coating is sprayed on the metal substrate after sandblasting and roughened by the prior art. The spraying current is 150-180A, the spraying voltage is 30-32V, and the spraying Air pressure 0.55MP, spraying distance 150mm. The thickness of the sprayed layer is 10mm, and the Rockwell hardness of the surface of the sprayed layer is about 61 (HR45N). Th...
PUM
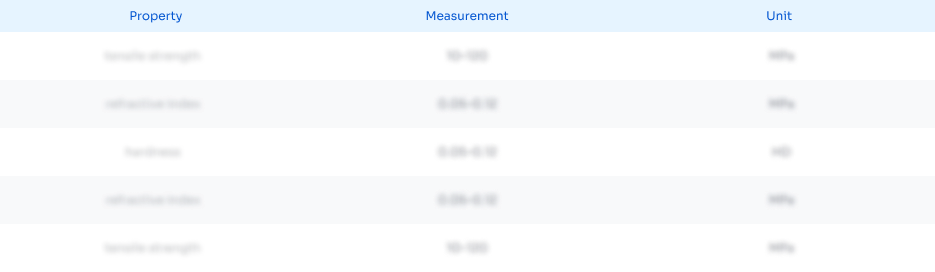
Abstract
Description
Claims
Application Information

- R&D
- Intellectual Property
- Life Sciences
- Materials
- Tech Scout
- Unparalleled Data Quality
- Higher Quality Content
- 60% Fewer Hallucinations
Browse by: Latest US Patents, China's latest patents, Technical Efficacy Thesaurus, Application Domain, Technology Topic, Popular Technical Reports.
© 2025 PatSnap. All rights reserved.Legal|Privacy policy|Modern Slavery Act Transparency Statement|Sitemap|About US| Contact US: help@patsnap.com