Heat synthesis preparation method for maleic anhydride grafted ethene-octylen copolymer
An octene copolymer and maleic anhydride technology, applied in the field of polymer science, can solve the problems of complex reaction conditions and devices, low grafting rate, uneven reaction, etc., and achieve the convenience of large-scale production, simple reaction equipment, and extensive The effect of applying the foreground
- Summary
- Abstract
- Description
- Claims
- Application Information
AI Technical Summary
Problems solved by technology
Method used
Examples
Embodiment 1
[0013] Add 5g of ethylene-octene resin, 0.5g of maleic anhydride, and 60mg of dibenzoyl peroxide into the autoclave, then put 50ml of xylene into the autoclave, tighten the lid of the autoclave and place it in a constant temperature oven at 160°C for 6 hour, then cooled with water, opened the autoclave, the solution was poured in the ethylene glycol of 250ml, stirred (rotating speed 150 rev / min) 1 hour on the magnetic stirrer, to remove the unreacted material, then suction filtration, the suction The powder obtained by filtration was dried in a vacuum oven at 70°C for 8 hours to obtain an ethylene-octene-maleic anhydride graft copolymer with a graft ratio of 5.3%wt.
Embodiment 2
[0015] Add 10g of ethylene-octene resin, 2g of maleic anhydride, 135mg of tert-butyl peroxybenzoate and 1g of acrylic acid into the autoclave, then put in 50ml of dimethyl sulfoxide, tighten the lid of the autoclave and place it in a 210°C In constant temperature oven, place 12 hours, then cool with water, open autoclave, solution is poured in the ethylene glycol of 300ml, stir (rotating speed 300 revs / min) 1 hour on magnetic stirrer, to remove unreacted substance, Then it was filtered by suction, and the powder obtained by suction filtration was dried in a vacuum oven at 80° C. for 28 hours to obtain an ethylene-octene-maleic anhydride graft copolymer with a graft rate of 5.7%wt.
Embodiment 3
[0017] Add 5g of ethylene-octene resin, 1.5g of maleic anhydride, 200mg of dicumyl peroxide and 1.5g of α-methyl methacrylate into the autoclave, then add 50ml of benzene, tighten the lid of the autoclave and put In a constant temperature oven at 160°C, place it for 24 hours, then cool it with water, open the autoclave, pour the solution into 300ml of ethylene glycol, stir on a magnetic stirrer (500 rpm) for 1 hour, to remove unreacted material, then suction-filtered, and the powder obtained by suction-filtration was dried in a vacuum oven at 80°C for 12 hours to obtain an ethylene-octene-maleic anhydride graft copolymer with a graft rate of 6.8%wt.
[0018] The maleic anhydride grafted ethylene-octene copolymer prepared by the method of the present invention is used as a compatibilizer for ethylene-octene and nylon blending, so that the flexibility of the blend is greatly improved; the prepared maleic anhydride grafted Ethylene-octene copolymer is used as a compatibilizer for...
PUM
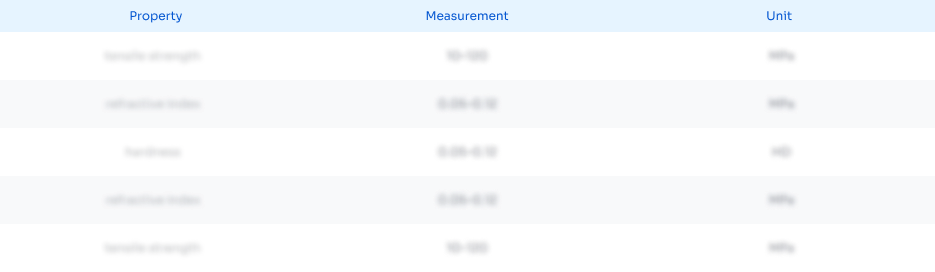
Abstract
Description
Claims
Application Information

- R&D
- Intellectual Property
- Life Sciences
- Materials
- Tech Scout
- Unparalleled Data Quality
- Higher Quality Content
- 60% Fewer Hallucinations
Browse by: Latest US Patents, China's latest patents, Technical Efficacy Thesaurus, Application Domain, Technology Topic, Popular Technical Reports.
© 2025 PatSnap. All rights reserved.Legal|Privacy policy|Modern Slavery Act Transparency Statement|Sitemap|About US| Contact US: help@patsnap.com