Electrohydraulic servo pressure-torque coupling three-way vibration loading tree-axis instrument
An electro-hydraulic servo and electro-hydraulic servo valve technology, which is applied to instruments, scientific instruments, measuring devices, etc., can solve the problems of difficult to achieve static and dynamic stress coupling changes, large changes in gas compression volume, and difficult to achieve automatic control, etc. Mutual interference, reduction of equipment manufacturing cost, effect of eliminating gaps
- Summary
- Abstract
- Description
- Claims
- Application Information
AI Technical Summary
Problems solved by technology
Method used
Image
Examples
Embodiment Construction
[0024] Below in conjunction with accompanying drawing and embodiment the present invention will be described in further detail:
[0025] Such as figure 1 As shown, the main engine includes a pressure chamber 1 arranged on the upper part of the frame horizontal plate 5, a lifting arm 15 placed next to the pressure chamber 1 and fixed on the frame horizontal plate 5 and a lifting mechanism 14 at its upper end, and a base box 24 The upper axial pressure mechanism 8, the torsion mechanism 4 coaxially connected with the axial pressure mechanism 8, the pressure torsion connection mechanism 2 placed between the pressure chamber 1 and the torsion mechanism 4, the balance cylinder 10 placed in the base box 24 and the The lateral pressure mechanism 11 outside the base box 24; the axial pressure mechanism 8 includes a main shaft 19, an axial pressure driver 20 coaxially connected with the main shaft, and an axial pressure sensor arranged at the upper end of the axial pressure driver 20 a...
PUM
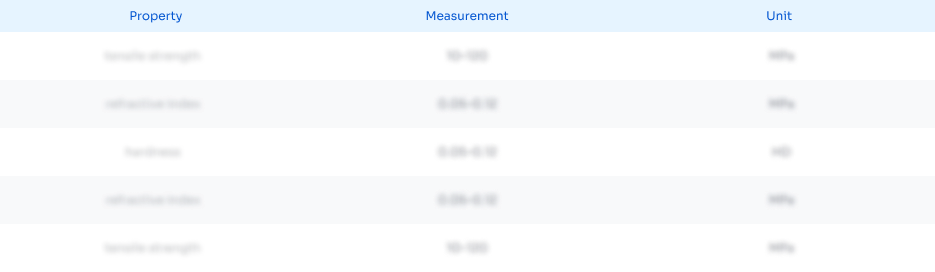
Abstract
Description
Claims
Application Information

- Generate Ideas
- Intellectual Property
- Life Sciences
- Materials
- Tech Scout
- Unparalleled Data Quality
- Higher Quality Content
- 60% Fewer Hallucinations
Browse by: Latest US Patents, China's latest patents, Technical Efficacy Thesaurus, Application Domain, Technology Topic, Popular Technical Reports.
© 2025 PatSnap. All rights reserved.Legal|Privacy policy|Modern Slavery Act Transparency Statement|Sitemap|About US| Contact US: help@patsnap.com