Process for producing Mg rare earth intermediate alloy by Submerged Liquid Cathode electrolysis under low-temperature
A rare earth intermediate alloy and liquid cathode technology, applied in the field of molten salt electrolysis metallurgy, can solve problems such as poor collection, discontinuous production, and current efficiency drop, and achieve the effects of high energy utilization rate and uniform composition
- Summary
- Abstract
- Description
- Claims
- Application Information
AI Technical Summary
Problems solved by technology
Method used
Examples
Embodiment 1
[0013] With commercially available chemically pure potassium chloride and sodium chloride, 8~30wt% (LPC)CL after dehydration 3 As a raw material, weigh 10% of LPCCl by weight % 3 50% KCl; 40% NaCl as electrolyte, preheated at 100°C for 3 hours, fully mixed with another raw material magnesium-5wt% lanthanum-praseodymium-cerium master alloy, the ratio of its mass to total electrolyte is 1:4 , put it into a cylindrical open electrolytic crucible with a diameter of 10cm and a height of 16cm, raise the temperature to 700-900°C, and start electrolysis after the added electrolyte melts. Stir properly during the electrolysis process, and leave the furnace for a period of time at the end of the electrolysis to control the furnace temperature at 750°C to produce the magnesium-lanthanum-praseodymium-cerium master alloy. The rare earth content of lanthanum, praseodymium and cerium in the alloy is 18wt%, and the current efficiency reaches 71%.
Embodiment 2
[0015] With commercially available chemically pure potassium chloride and sodium chloride, 8~30wt% (LPC)CL after dehydration 3 As a raw material, weigh 15% of LPCCl by weight % 3 The KCl of 48%; The NaCl of 37% is as electrolyte, through 100 ℃ of preheating 3 hours, fully mix again and another kind of raw material magnesium-6wt% lanthanum praseodymium cerium master alloy, its quality and total electrolyte are 1: 4.5, Put it into a cylindrical open electrolytic crucible with a diameter of 10cm and a height of 16cm, raise the temperature to 700-900°C, and start electrolysis after the added electrolyte melts. Proper stirring during the electrolysis process, and standing for a period of time at the end of the electrolysis so that the temperature of the furnace is controlled at 780°C and the product is released from the furnace to prepare a magnesium-lanthanum-praseodymium-cerium master alloy. The rare earth content of lanthanum, praseodymium and cerium in the alloy is 25 wt%, and...
Embodiment 3
[0017] With commercially available chemically pure potassium chloride and sodium chloride, 8~30wt% (LPC)CL after dehydration 3 As a raw material, weigh 25% of LPCCl by weight % 3 ;: 45% KCl; 30% NaCl as electrolyte, preheated at 200°C for 3 hours, fully mixed with another raw material magnesium-8wt% lanthanum-praseodymium-cerium master alloy, its quality and total electrolyte are 1:5 , put it into a cylindrical open electrolytic crucible with a diameter of 10cm and a height of 16cm, raise the temperature to 700-900°C, and start electrolysis after the added electrolyte melts. Proper stirring during the electrolysis process, and standing for a period of time at the end of the electrolysis to control the temperature of the product out of the furnace at 820°C to prepare the magnesium-lanthanum-praseodymium-cerium master alloy. The rare earth content of lanthanum, praseodymium and cerium in the alloy is 30 wt%, and the current efficiency reaches 73%.
PUM
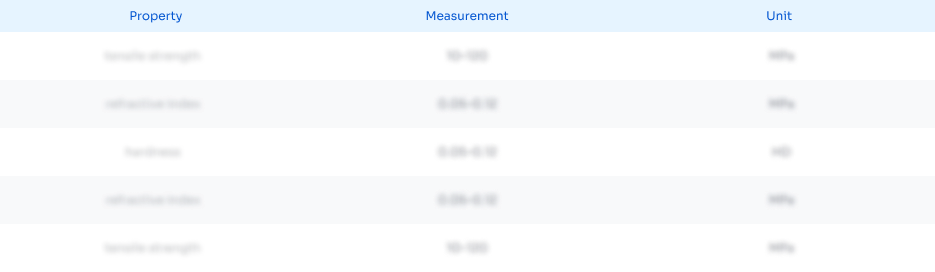
Abstract
Description
Claims
Application Information

- R&D
- Intellectual Property
- Life Sciences
- Materials
- Tech Scout
- Unparalleled Data Quality
- Higher Quality Content
- 60% Fewer Hallucinations
Browse by: Latest US Patents, China's latest patents, Technical Efficacy Thesaurus, Application Domain, Technology Topic, Popular Technical Reports.
© 2025 PatSnap. All rights reserved.Legal|Privacy policy|Modern Slavery Act Transparency Statement|Sitemap|About US| Contact US: help@patsnap.com