Method for preparing amide using nonhomogeneous phase oximation rearrangement
An amide and rearrangement technology, which is applied in chemical instruments and methods, the preparation of organic compounds, and the preparation of carboxylic acid amides, can solve the problems of high material viscosity, high cost, and high energy consumption, and reduce sulfuric acid consumption and by-products , high conversion rate and yield, and the effect of lowering the reaction temperature
- Summary
- Abstract
- Description
- Claims
- Application Information
AI Technical Summary
Problems solved by technology
Method used
Examples
Embodiment 1
[0044] Example 1: Add 45.0 g of n-hexane, 15.2 g of methyl ethyl ketone, and 1.5 g of titanium-silicon molecular sieve in advance in a 250 ml glass reactor with magnetic stirring. After mixing fully, the temperature is raised to 65° C., and 27.5% (by weight) hydrogen peroxide 28.0 g is slowly added dropwise. g and 25% (weight ratio) ammoniacal liquor 30.0g. Add dropwise at a constant speed for 2.5 hours, and continue to react for 1 hour. Stirring was maintained during the reaction, and the temperature was controlled at 65°C. After cooling and standing to separate the heavy phase, extract it three times with 45.0 g of n-hexane, and mix the extraction phase with the light phase of the reaction to obtain 105.6 g of methyl ethyl ketone oxime-n-hexane solution. %, the selectivity of methyl ethyl ketone oxime is 97.1%. Add SO to another 250ml reactor 3 Concentration is 5% oleum 15.8g, slowly add methyl ethyl ketoxime oxime solution dropwise. The reaction temperature is 68° C., a...
Embodiment 2
[0045] Embodiment 2: Add cyclohexane, cyclohexanone and titanium silicon molecular sieve catalyst in advance in the glass reactor of 250ml band magnetic stirring, cyclohexane consumption is cyclohexane: cyclohexanone=3.0: 1 (molar ratio, below Same), the mass percentage of titanium silicon molecular sieve is 2.2%. When the temperature rises to 70-71° C., hydrogen peroxide and ammonia water are added dropwise for oximation reaction. The total consumption of hydrogen peroxide and ammonia is hydrogen peroxide: ammonia: cyclohexanone=1.1:1.9:1. The dropwise addition time was 2 hours, and the reaction was continued for 1.1 hours after the dropwise addition was completed. Stirring was maintained during the reaction, and the temperature was controlled at 71°C. The aqueous phase product of the reaction is extracted three times with cyclohexane equivalent to the reaction volume, and the extract phase is mixed with the organic phase product of the reaction to obtain a cyclohexane solut...
Embodiment 3
[0047] Example 3: 39.2 g of cyclohexane, 15.1 g of cyclohexanone, and 3.8 g of titanium-silicon molecular sieve catalyst were added into a 250 ml glass reactor. Take 23.5 g of hydrogen peroxide and 33.2 g of ammonia water with a concentration of 27.5% (weight ratio) respectively, and add them dropwise into the reaction kettle at a uniform speed, and the feeding time is 2.1 hours. Magnetic stirring is adopted, the temperature is controlled by an oil bath, and the reaction temperature is about 72°C under normal pressure. After the addition, the reaction was continued for 1 hour, cooled and left to stand, and 55.1 g of the light phase was separated, and the heavy phase was extracted three times in equal parts with 39.0 g of cyclohexane, and the extracted phase was mixed with the light phase to obtain 95.3 g of cyclohexanone oxime solution. Add SO to another 250ml reactor 3 Concentration is 15.8g of fuming sulfuric acid of 8%, and cyclohexanone oxime solution is slowly added drop...
PUM
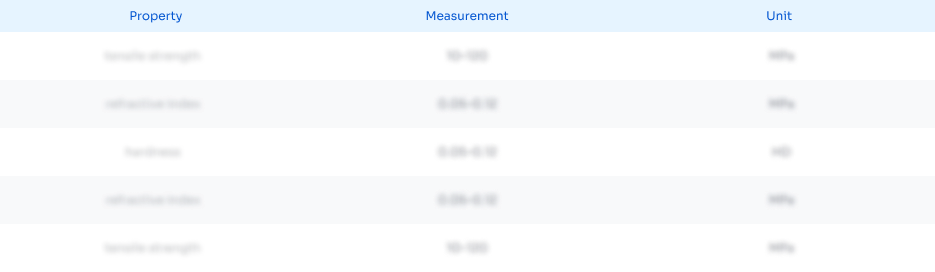
Abstract
Description
Claims
Application Information

- R&D
- Intellectual Property
- Life Sciences
- Materials
- Tech Scout
- Unparalleled Data Quality
- Higher Quality Content
- 60% Fewer Hallucinations
Browse by: Latest US Patents, China's latest patents, Technical Efficacy Thesaurus, Application Domain, Technology Topic, Popular Technical Reports.
© 2025 PatSnap. All rights reserved.Legal|Privacy policy|Modern Slavery Act Transparency Statement|Sitemap|About US| Contact US: help@patsnap.com