Method for producing surface compound cutter billet by horizontal electro-slag surfacing
A technology of electroslag surfacing and surface compounding, which is applied in manufacturing tools, arc welding equipment, welding equipment, etc., can solve the problems of high surface treatment requirements, unsuitable composite steel, and unsatisfactory adhesion, so as to improve the comprehensive mechanical properties. , low cost, and the effect of improving the use value
- Summary
- Abstract
- Description
- Claims
- Application Information
AI Technical Summary
Problems solved by technology
Method used
Image
Examples
Embodiment Construction
[0020] Take Q235 plain carbon steel as the body steel and W18Cr14V1 or W6M05Cr4V2 high-speed tool steel surface composite mechanical blade composite flat steel as an example:
[0021] The size of the body steel that needs electroslag surfacing is 70×140mm as shown in Figure 3, and a gap on one side can also be processed according to the process requirements. For example, the gap is trapezoidal, the upper bottom is 55mm, the lower bottom is 50mm, and the height is 25mm. The processed and cleaned body steel is placed horizontally on the working platform, fixed by four water-passing templates, and cooled by water. Three of the water-passing templates can be translated synchronously with the working platform, and the flat steel of high-speed steel is made into double-headed or triple-headed electrodes, connected in parallel, and slowly moved to the top of the main body steel to keep a certain distance between the electrodes and the surroundings. Putting in the electroslag liquid m...
PUM
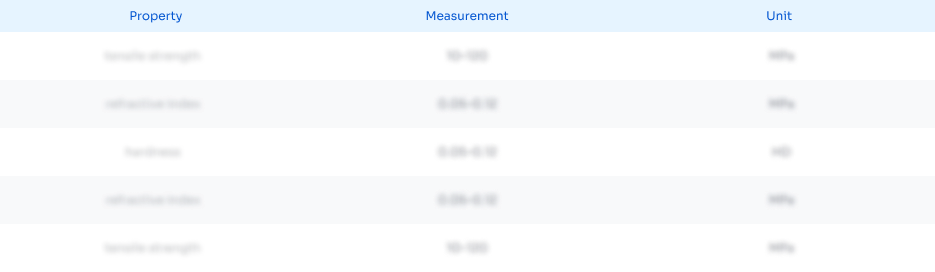
Abstract
Description
Claims
Application Information

- R&D
- Intellectual Property
- Life Sciences
- Materials
- Tech Scout
- Unparalleled Data Quality
- Higher Quality Content
- 60% Fewer Hallucinations
Browse by: Latest US Patents, China's latest patents, Technical Efficacy Thesaurus, Application Domain, Technology Topic, Popular Technical Reports.
© 2025 PatSnap. All rights reserved.Legal|Privacy policy|Modern Slavery Act Transparency Statement|Sitemap|About US| Contact US: help@patsnap.com