Method for preparing alloy sheet
A thin plate and alloy technology, which is applied in the field of improvement of the process of preparing alloy thin plates
- Summary
- Abstract
- Description
- Claims
- Application Information
AI Technical Summary
Problems solved by technology
Method used
Image
Examples
specific Embodiment approach 1
[0005] Embodiment 1: This embodiment is achieved through the following steps: 1. Prepare the material rods and substrates to be evaporated; 2. Put the material rods to be evaporated into water-cooled copper crucibles respectively, and install the substrates on the substrate shafts , and evacuate the vacuum chamber to 1~5×10 -3 Pa; 3. Set the process parameters; 4. Adjust the heating substrate to the specified temperature; 5. Heating and evaporating the separation layer rod to deposit the separation layer; 6. Stop the deposition of the separation layer, heat and evaporate the metal alloy rod, and deposit the metal alloy Seventh, stop the electron gun heating, wait for the temperature to drop, take out the substrate, and separate the metal alloy layer from the substrate to obtain an alloy sheet. The material rod to be evaporated in the step 1 includes a separation layer material rod and an alloy rod; the substrate material in the step 1 is low carbon steel or stainless steel, an...
specific Embodiment approach 2
[0006] Specific implementation mode two: (see Figure 1 ~ Figure 4 ) This specific embodiment first prepares superalloy GH4169 bar and separation layer material ZrO 2 . GH4169 bar diameter is Φ98.5±0.5mm, length 300, the length of the bar depends on the equipment, and the material must be dense and free of pores, which can prevent splashing during metal melting and evaporation, which will affect the surface quality of the deposited thin plate. Therefore, the GH4169 ingot is best prepared by vacuum smelting method, and then processed to the specified size by lathe. ZrO 2 The diameter of the bar is Φ68.5±0.5mm, and the length is 200mm. It is usually prepared by vacuum hot pressing and sintering. Before loading, turn on the circulating water and preheat the diffusion vacuum pump at the same time. Then start to load the rod material for evaporation, put two GH4169 rods into the third water-cooled copper crucible g3 and the fourth water-cooled copper crucible g4 respectively, t...
specific Embodiment approach 3
[0007] Specific implementation mode three: (see Figure 1 ~ Figure 4 ) The material composition (percentage by weight) of preparing Fe-based ODS alloy sheet in this specific embodiment is 73.5% Fe, 20% Cr, 5.5% Al, 1% Y 2 o 3 . First prepare the material to be evaporated FeCrAl alloy rod, Y 2 o 3 Rod and separation layer material ZrO 2 . The diameter of the FeCrAl rod is Φ98.5±0.5mm, and the length is 30-500mm. It is best to use vacuum smelting for the FeCrAl rod. Y 2 o 3 The diameter of the bar is Φ68.5±0.5mm, the length is 20-500mm, prepared by vacuum hot pressing and sintering, ZrO 2The size and production process of the bar are the same as in the second embodiment. Before loading, turn on the circulating water and preheat the diffusion vacuum pump at the same time. Then start to load the rods for evaporation, put 2 GH4169 rods into the third water-cooled copper crucible g3 and the fourth water-cooled copper crucible g4 respectively, one ZrO 2 Put the rod into th...
PUM
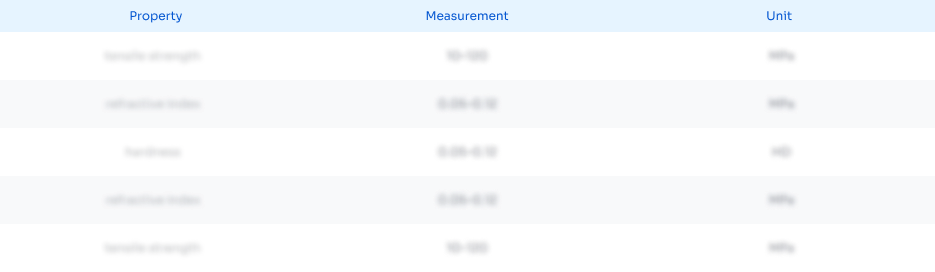
Abstract
Description
Claims
Application Information

- R&D
- Intellectual Property
- Life Sciences
- Materials
- Tech Scout
- Unparalleled Data Quality
- Higher Quality Content
- 60% Fewer Hallucinations
Browse by: Latest US Patents, China's latest patents, Technical Efficacy Thesaurus, Application Domain, Technology Topic, Popular Technical Reports.
© 2025 PatSnap. All rights reserved.Legal|Privacy policy|Modern Slavery Act Transparency Statement|Sitemap|About US| Contact US: help@patsnap.com