Stimulating responsiveness porous hollow gel fiber and its producing method
A hollow gel fiber, stimuli-responsive technology, applied in the field of stimuli-responsive porous hollow gel fiber and its manufacturing, can solve the problems of application limitation, poor mechanical properties, etc.
- Summary
- Abstract
- Description
- Claims
- Application Information
AI Technical Summary
Problems solved by technology
Method used
Image
Examples
Embodiment 1
[0034] Add dry PAN powder with a viscosity-average molecular weight of 90,000 and polyvinylpyrrolidone (PVP) into dimethylacetamide (DMAc), swell at 60°C for 1 hour, and dissolve at 70°C for 1 hour under temperature program control to obtain A PAN-DMAc-PVP solution (PAN:PVP=9:1) containing 14% (weight percent) of polymer was filtered and vacuum defoamed for 8 hours.
[0035] The spinning solution enters the coagulation bath from the inserted tube spinneret through the metering pump, the coagulation bath is an aqueous solution containing 10% (weight percent) DMAc, and the bath temperature is 8°C. After the as-spun fibers were extracted from the coagulation bath, they were introduced into a water bath at 65°C and a water bath at 95°C for secondary stretching, with a total stretching ratio of 8 times. Then washed with water and dried in an oven at 100°C to obtain a PAN-based porous hollow fiber.
[0036] The PAN-based porous hollow fiber prepared by wet spinning is oxidized in a...
Embodiment 2
[0040] Add dry PAN powder with a viscosity-average molecular weight of 50,000 and polyethylene glycol (PEG) with a viscosity-average molecular weight of 20,000 into dimethylformamide (DMF), swell at 60°C for 1 hour under temperature program control, and then Dissolved for 1 hour to prepare a PAN-DMF-PEG solution (PAN:PEG=5:1) containing 17% (weight percent) of polymer, filtered, and vacuum defoamed for 8 hours.
[0041] The spinning solution enters the coagulation bath from the inserted tube spinneret through the metering pump, the coagulation bath is water, and the bath temperature is 70°C. After the as-spun fibers were extracted from the coagulation bath, they were introduced into a water bath at 65°C, a hot water bath and steam at 128°C for secondary stretching, with a total stretching ratio of 5 times. Then washed with water and dried in an oven at 100°C to obtain a PAN-based porous hollow fiber.
[0042] The PAN-based porous hollow fiber prepared by wet spinning is oxidi...
Embodiment 3
[0046] Add dry PAN powder with a viscosity-average molecular weight of 170,000 and polyvinyl alcohol (PVA) with a viscosity-average molecular weight of 1700 into dimethyl sulfoxide (DMSO), and swell at 60°C for 1 hour under temperature program control. Dissolved for 1 hour to prepare a PAN-DMAc-PVA solution (PAN:PVA=9:1) containing 14% (weight percent) of polymer, filtered, and vacuum defoamed for 8 hours.
[0047] The spinning solution enters the coagulation bath from the inserted tube spinneret through the metering pump, the coagulation bath is an aqueous solution containing 5% (weight percent) DMSO, and the bath temperature is 8°C. After the as-spun fibers were extracted from the coagulation bath, they were introduced into a water bath at 65°C and a water bath at 98°C for secondary stretching, with a total stretching ratio of 8 times. Then washed with water and dried in an oven at 100°C to obtain a PAN-based porous hollow fiber.
[0048] The PAN-based porous hollow fiber p...
PUM
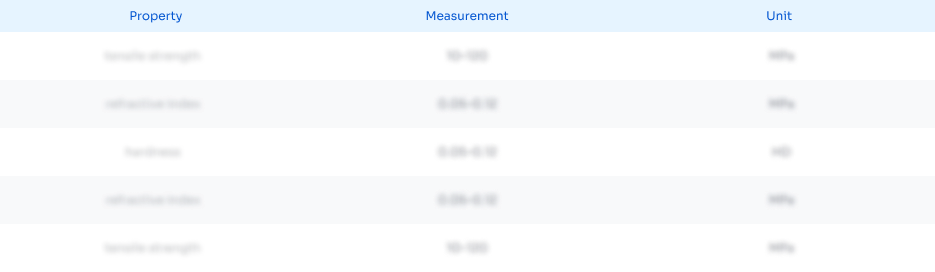
Abstract
Description
Claims
Application Information

- R&D
- Intellectual Property
- Life Sciences
- Materials
- Tech Scout
- Unparalleled Data Quality
- Higher Quality Content
- 60% Fewer Hallucinations
Browse by: Latest US Patents, China's latest patents, Technical Efficacy Thesaurus, Application Domain, Technology Topic, Popular Technical Reports.
© 2025 PatSnap. All rights reserved.Legal|Privacy policy|Modern Slavery Act Transparency Statement|Sitemap|About US| Contact US: help@patsnap.com