Production of Nd doped high silicon-oxygen laser glass
A technology of high silica glass and laser glass, applied in the field of laser glass, can solve the problems of poor chemistry and thermal shock resistance of phosphoric acid glass, difficult to increase the concentration of neodymium doping, and limited application.
- Summary
- Abstract
- Description
- Claims
- Application Information
AI Technical Summary
Problems solved by technology
Method used
Examples
Embodiment 1
[0030] After decomposing, it is equivalent to 0.25g of Nd 2 o 3 0.65g of analytically pure Nd(NO 3 ) 3 ·6H 2 O was put into 25 ml of deionized water solution, and after it was completely dissolved, the SiO 2 The porous glass with a content of 97wt% is put into the solution and soaked for more than 10 minutes, and the Nd in the glass after sintering 2 o 3 The weight percentage is about 0.23wt%; after that, put the high-silica microporous glass doped with neodymium ions into a high-temperature furnace, and undergo solid-phase sintering at a temperature of 1050-1200°C in air or oxygen to eliminate micropores and become dense and transparent high silica glass. During the sintering process, raise from room temperature to 950°C at a speed of 10°C per minute, then rise from this temperature to 1100-1200°C at a speed of 5°C per minute and keep it at this temperature for more than 30 minutes, then turn off The power supply of the high temperature furnace allows the glass to cool...
Embodiment 2
[0032] Will be decomposed equivalent to 2.5g of Nd 2 o 3 6.5g of analytically pure Nd(NO 3 ) 3 ·6H 2 O is put into 25 ml of ethanol or deionized water solution, after it is completely dissolved, and then the size is 5 × 5 × 3mm, SiO 2 The porous glass with a content of more than 97wt% is put into the solution and soaked for more than 10 minutes; after that, the microporous glass is put into a high-temperature furnace, and the Nd(NO 3 ) 3 ·6H 2 After O is fully decomposed, it is cooled with the furnace. In the same way, this process was repeated twice. After that, the Nd in the glass sintered three times with neodymium ions 2 o 3 The high-silica microporous glass with a weight percentage of about 6.9wt% is placed in a high-temperature furnace, and undergoes solid-state sintering at a temperature of 1050-1200°C in air or oxygen to eliminate micropores and become a dense and transparent high-silica glass . During the sintering process, the temperature is raised from ro...
Embodiment 3
[0034] Will be decomposed equivalent to 1.3g of Nd 2 o 3 3.4g of analytically pure Nd(NO 3 )3 ·6H 2 O and 3.75g analytically pure Y (NO 3 ) 3 ·6H 2 O and 6.1g of analytically pure Al(NO 3 ) 3 9H 2 O was put into 25 ml of 1 N nitric acid solution, and after it was completely dissolved, the SiO 2 The porous glass with a content of more than 97% (by weight percent) is put into the solution and soaked for more than 10 minutes; after that, the high-silica microporous glass doped with these ions is put into a high-temperature furnace, and passed through in air or oxygen. The solid-phase sintering at a temperature of 1120°C eliminates micropores and becomes dense and transparent high-silica glass. During the sintering process, the temperature is raised from room temperature to 950°C at a rate of less than 10°C per minute. Then, raise the temperature from 950°C to 1120°C at a rate of less than 5°C per minute and keep the temperature at 1120°C for 30 minutes, then turn off th...
PUM
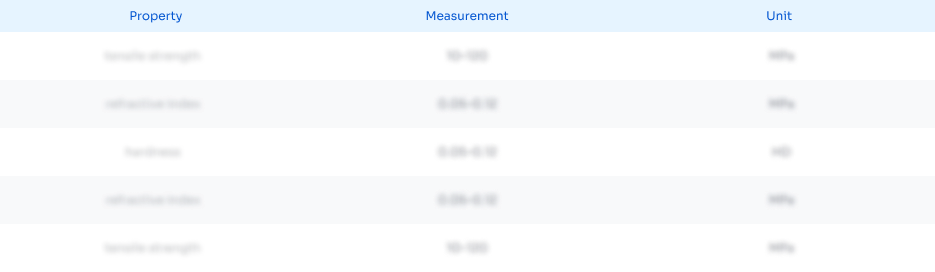
Abstract
Description
Claims
Application Information

- R&D Engineer
- R&D Manager
- IP Professional
- Industry Leading Data Capabilities
- Powerful AI technology
- Patent DNA Extraction
Browse by: Latest US Patents, China's latest patents, Technical Efficacy Thesaurus, Application Domain, Technology Topic, Popular Technical Reports.
© 2024 PatSnap. All rights reserved.Legal|Privacy policy|Modern Slavery Act Transparency Statement|Sitemap|About US| Contact US: help@patsnap.com