Built-in type jet nozzle for laser melting and coating
A laser cladding and built-in technology, which is applied in the direction of fusion spraying, laser welding equipment, manufacturing tools, etc., can solve the problems of inconvenient processing, high surface of parts, and difficult manual operation by operators, so as to solve the problem of burning and Effects of damage, improvement of service life, and cost reduction
- Summary
- Abstract
- Description
- Claims
- Application Information
AI Technical Summary
Problems solved by technology
Method used
Image
Examples
Embodiment Construction
[0022] The present invention will be further described in detail below in conjunction with examples and drawings.
[0023] As shown in the figure, the wall of the tapered cylinder is provided with a powder channel 4, a cooling water channel 10 and a protective gas channel. The cone body is composed of upper and lower parts, namely, the upper cone 1 and the lower cone formed by the lower inner cone 5 and the lower cone sleeve 6. The upper cone cylinder 1 and the lower cone sleeve 6 are connected by threads and are positioned by positioning pins. The powder channel inlets 3 are distributed on the upper circumference of the upper cone 1, and the powder channel outlets 7 are evenly distributed on the lower circumference of the lower cone. The angle between the axis of the connecting part of the powder passage 4 and its inlet 3 and the center axis of the nozzle is between 30-70°. A cooling water ring 12 is built in the bottom of the lower inner cone 5, and the cooling water ring 12 is ...
PUM
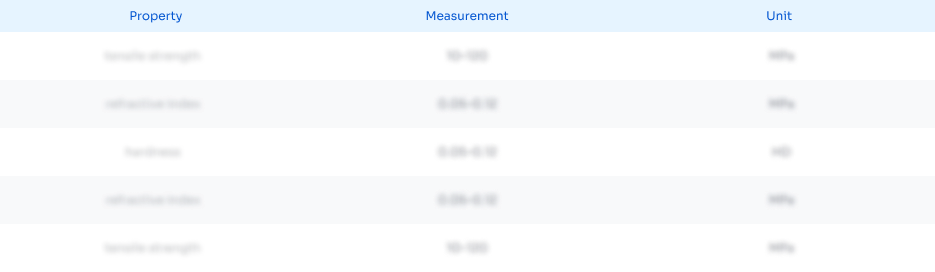
Abstract
Description
Claims
Application Information

- Generate Ideas
- Intellectual Property
- Life Sciences
- Materials
- Tech Scout
- Unparalleled Data Quality
- Higher Quality Content
- 60% Fewer Hallucinations
Browse by: Latest US Patents, China's latest patents, Technical Efficacy Thesaurus, Application Domain, Technology Topic, Popular Technical Reports.
© 2025 PatSnap. All rights reserved.Legal|Privacy policy|Modern Slavery Act Transparency Statement|Sitemap|About US| Contact US: help@patsnap.com