Method for preparing flame-resisting polyester in phosphorus series
A manufacturing method and technology of phosphorus-based flame retardants, which are applied in the field of manufacturing phosphorus-based flame-retardant copolyesters, can solve the problems of many reaction steps, long process routes, and many types of raw materials used, and achieve low cost and short process routes , the effect of fewer types of raw materials
- Summary
- Abstract
- Description
- Claims
- Application Information
AI Technical Summary
Problems solved by technology
Method used
Image
Examples
Embodiment 1
[0026] 1. The first step is to prepare a mixture of ethylene glycol propionate-based phenylphosphate, 2-carboxyethylphenylphosphoric acid and ethylene glycol flame retardant:
[0027] Take 45kg of commercially available 2-carboxyethylphenylphosphoric acid containing 14.5% of phosphorus and 2% of water, and 55kg of ethylene glycol, and add them to the esterification kettle, and gradually raise the temperature to 165°C under stirring, and carry out under normal pressure conditions. Esterification reaction, properly increase the reaction temperature to 170°C before the end of the esterification, collect the distilled water to reach 7.6kg, take the reaction product to measure the acid value to control and determine the desired reaction end point, the esterification rate is 90%, filter for later use . The product is a mixture of ethylene glycol propionate-based phenylphosphate, 2-carboxyethylphenylphosphoric acid and ethylene glycol flame retardant, which contains ethylene glycol p...
Embodiment 2
[0031] 1. The first step is to prepare a mixture of ethylene glycol propionate-based phenylphosphate, 2-carboxyethylphenylphosphoric acid and ethylene glycol flame retardant: the method is the same as in Example 1.
[0032] 2. The second step, polymerization of flame retardant polyester:
[0033] Get 200kg of purified terephthalic acid (PTA) and 185kg of ethylene glycol (EG). The esterification process conditions and operation method are the same as in Example 1. After the esterification product is moved into the polycondensation tank, add the new flame retardant made in the first step 20kg of mixed solution (wherein containing EG6.9kg) is put in the polymerization kettle, and catalyst, auxiliary agent addition, polycondensation process condition and operating method are the same as embodiment one, obtain the required flame retardant polyester chip of the present invention. The phosphorus content in the flame-retardant polyester chip was 5560 ppm.
Embodiment 3
[0035] 1. The first step is to prepare the mixed solution of ethylene glycol propionate, ethylene glycol phenylphosphate, 2-carboxyethylphenylphosphoric acid and ethylene glycol:
[0036] Take 45kg of commercially available 2-carboxyethylphenylphosphoric acid containing 14.5% of phosphorus and 2% of water, and 55kg of ethylene glycol, and add them to the esterification kettle, and gradually raise the temperature to 165°C under stirring, and carry out under normal pressure conditions. Esterification reaction, properly increase the reaction temperature to 170°C before the end of the esterification, collect the distilled water to reach 6.1kg, take the reaction product to measure the acid value to control and determine the desired reaction end point, the esterification rate is 70%, filter for later use . The product is a mixture of ethylene glycol propionate-based phenylphosphate, 2-carboxyethylphenylphosphoric acid and ethylene glycol, which contains ethylene glycol propionate-ba...
PUM
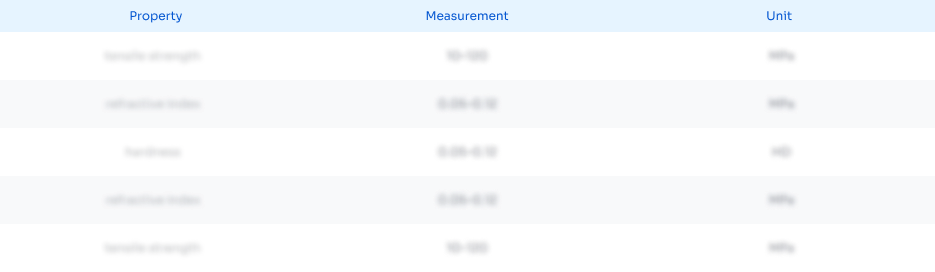
Abstract
Description
Claims
Application Information

- R&D
- Intellectual Property
- Life Sciences
- Materials
- Tech Scout
- Unparalleled Data Quality
- Higher Quality Content
- 60% Fewer Hallucinations
Browse by: Latest US Patents, China's latest patents, Technical Efficacy Thesaurus, Application Domain, Technology Topic, Popular Technical Reports.
© 2025 PatSnap. All rights reserved.Legal|Privacy policy|Modern Slavery Act Transparency Statement|Sitemap|About US| Contact US: help@patsnap.com