Method for preparing titanium diboride dispersion-strengthened Cu-base composites by using mechanical alloying method
A technology of dispersion strengthening copper and titanium diboride, which is applied in the field of metal matrix composite material preparation, can solve the problems of high production cost, complicated preparation process of ultrafine powder, and many preparation processes
- Summary
- Abstract
- Description
- Claims
- Application Information
AI Technical Summary
Problems solved by technology
Method used
Examples
Embodiment 1
[0012] Example 1: Cu powder and TiO with a particle size of 150 mesh and a purity of 99.9% 2 Pink, B 2 O 3 Powder and Mg powder as raw materials, the Cu powder, TiO 2 Pink, B 2 O 3 Powder and Mg powder (Cu powder and TiO 2 +B 2 O 3 +Mg powder mass ratio is 95:5, of which TiO 2 , B 2 O 3 , Mg molar ratio is 1:1:5) Evenly mix, put the steel ball and mixed powder with the ball-to-material ratio of 20:1 into the high-energy ball mill ball mill tank in the glove box filled with argon, so that the ball-material mixture accounts for 15% of the volume of the inner cavity of the ball milling tank, high-energy ball milling at room temperature at 1000 rpm for 3 hours to form Cu and TiB 2 Mix the micro-powder ceramic material with MgO; then use hydrochloric acid with a concentration of 3mol / l to pickle the mixed powder for 12 hours at a temperature of 30°C to wash away the MgO to obtain Cu+TiB 2 Mixed powder; Cu+TiB 2 After the mixed powder is dried, put it into the ball mill jar of the high-...
Embodiment 2
[0013] Example 2: Using Cu powder and TiO with a particle size of 200 mesh and a purity of 99.9% 2 Pink, B 2 O 3 Powder and Mg powder as raw materials, the Cu powder, TiO 2 Pink, B 2 O 3 Powder and Mg powder (Cu powder and TiO 2 +B 2 O 3 +Mg powder mass ratio is 85:15, of which TiO 2 , B 2 O 3 , Mg molar ratio is 1:1:5) uniformly mix, put the steel ball and mixed powder with the ball-to-material ratio of 40:1 into the high-energy ball mill ball mill tank in the glove box filled with argon, so that the ball-material mixture accounts for 25% of the volume of the inner cavity of the ball milling tank, high-energy ball milling at 1500 rpm at room temperature for 9 hours to form Cu and TiB 2 Mix the micro-powder ceramic material with MgO; then use hydrochloric acid with a concentration of 2mol / l to pickle the mixed powder for 9h at a temperature of 55℃ to wash away the MgO to obtain Cu+TiB 2 Mixed powder; Cu+TiB 2 After the mixed powder is dried, put it into the ball mill jar of the hi...
Embodiment 3
[0014] Example 3: Cu powder and TiO with a particle size of 300 mesh and a purity of 99.9% 2 Pink, B 2 O 3 Powder and Mg powder as raw materials, the Cu powder, TiO 2 Pink, B 2 O 3 Powder and Mg powder (Cu powder and TiO 2 +B 2 O 3 +Mg powder mass ratio is 80:20, of which TiO 2 , B 2 O 3 , Mg molar ratio is 1:1:5) uniformly mix, put the steel ball and mixed powder with the ball-to-material ratio of 80:1 into the high-energy ball mill ball mill tank in the glove box filled with argon, so that the ball-to-material mixture accounts for 35% of the volume of the inner cavity of the ball milling tank, high-energy ball milling at room temperature at 2000 rpm for 15 hours to form Cu and TiB 2 Mix the micropowder ceramic material with MgO; then use hydrochloric acid with a concentration of 1mol / l to pickle the mixed powder for 3h at a temperature of 75℃ to wash away the MgO to obtain Cu+TiB 2 Mixed powder; Cu+TiB 2 After the mixed powder is dried, put it into the ball mill jar of the high-...
PUM
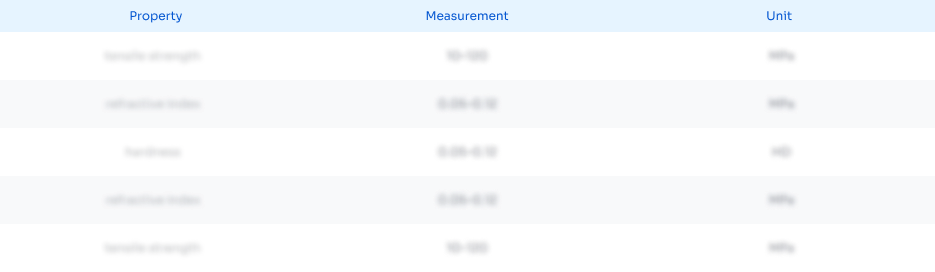
Abstract
Description
Claims
Application Information

- R&D Engineer
- R&D Manager
- IP Professional
- Industry Leading Data Capabilities
- Powerful AI technology
- Patent DNA Extraction
Browse by: Latest US Patents, China's latest patents, Technical Efficacy Thesaurus, Application Domain, Technology Topic, Popular Technical Reports.
© 2024 PatSnap. All rights reserved.Legal|Privacy policy|Modern Slavery Act Transparency Statement|Sitemap|About US| Contact US: help@patsnap.com