Industrial method of reusing waste plastics to produce gasoline and diesel oil
A technology of waste plastics and gasoline, applied in the petroleum industry, products, preparation of liquid hydrocarbon mixtures, etc., can solve the problems of high conversion rate of oil products, achieve the effect of increasing octane number and solving poor thermal conductivity
- Summary
- Abstract
- Description
- Claims
- Application Information
AI Technical Summary
Problems solved by technology
Method used
Image
Examples
Embodiment 1
[0032] The first step is to blend waste plastics polyethylene, polypropylene, and polystyrene in a ratio of 1:1:0.8, such as 100 kg of polyethylene, 100 kg of polypropylene, and 80 kg of polystyrene;
[0033] The second step is to push the waste plastics blended according to the above ratio into a tank-shaped or vertical reactor with a double-ribbon agitator inside and a molten salt as a heat-conducting medium jacket with a hydraulic propeller to heat, liquefy, and crack. The salt temperature is 450°C, and the heating liquefaction cracking temperature in the reactor is 350°C;
[0034] In the third step, the waste plastics in the reaction kettle are heated and cracked, and the materials produced by the reaction enter the visbreaker or other mild low-temperature cracking device for visbreaking distillation. The visbreaking temperature is 250°C, and the cracked gas is condensed by the condenser to form The liquid is sent to the rectification tower for rectification;
[0035]The ...
Embodiment 2
[0038] The first step is to blend waste plastics polyethylene and polystyrene in a ratio of 1:0.4, such as 100 kg of polyethylene and 40 kg of polystyrene;
[0039] The second step is to push the waste plastic blended according to the above ratio into a tank-shaped or vertical reactor with a double-ribbon agitator inside and a jacket of molten salt as a heat-conducting medium with a hydraulic propeller. Heating liquefaction and cracking, the molten salt temperature is 550°C, and the heating liquefaction temperature in the reactor is 450°C;
[0040] In the third step, the waste plastic in the reaction kettle is heated and cracked, and the material generated by the reaction enters the visbreaker or other mild low-temperature cracking device for visbreaking distillation. The visbreaking temperature is 300°C, and the cracked gas is condensed by the condenser to form The liquid is sent to the rectification tower for rectification;
[0041] The fourth step, at the same time, the mo...
Embodiment 3
[0044] In the first step, thermoplastic waste plastics such as polypropylene and polystyrene are blended in a ratio of 1:0.4, such as 100 kg of polypropylene and 40 kg of polystyrene;
[0045] The second step is to heat and liquefy the waste plastic blended according to the above ratio with a hydraulic propeller into a reaction kettle with a double ribbon agitator inside and a jacket with molten salt as a heat-conducting medium. The temperature of the molten salt is 500°C. The heating liquefaction temperature in the reaction kettle is 380°C,
[0046] In the third step, the waste plastics in the reaction kettle are heated and cracked, and the materials produced by the reaction are put into the visbreaker for visbreaking distillation. distillation;
[0047] The fourth step, at the same time, the molten plastic in the reactor is continuously pumped into the solid-liquid separation cylinder with molten salt separation liquid through the pump, and the residue and soil in the react...
PUM
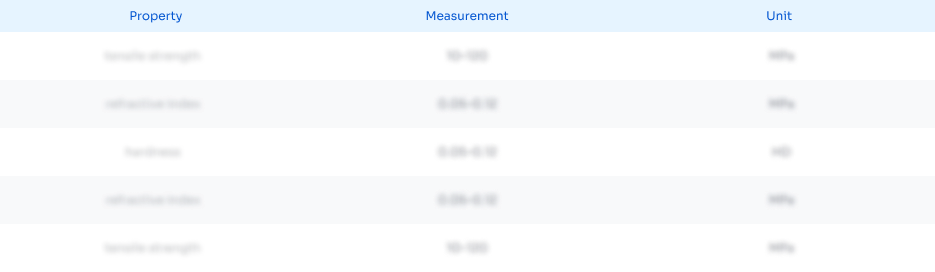
Abstract
Description
Claims
Application Information

- Generate Ideas
- Intellectual Property
- Life Sciences
- Materials
- Tech Scout
- Unparalleled Data Quality
- Higher Quality Content
- 60% Fewer Hallucinations
Browse by: Latest US Patents, China's latest patents, Technical Efficacy Thesaurus, Application Domain, Technology Topic, Popular Technical Reports.
© 2025 PatSnap. All rights reserved.Legal|Privacy policy|Modern Slavery Act Transparency Statement|Sitemap|About US| Contact US: help@patsnap.com