Process for preparing butyl butyrate
A butyl butyrate and catalyst technology, which is applied in the field of butyl butyrate preparation, can solve the problems of low catalyst activity and selectivity, and achieve the effects of reduced equipment investment, simplified process flow, and increased selectivity
- Summary
- Abstract
- Description
- Claims
- Application Information
AI Technical Summary
Problems solved by technology
Method used
Examples
Embodiment 2
[0025] Catalyst preparation example:
[0026] With 96.6 grams of copper nitrate (chemically pure, Beijing Chemical Plant), 300 grams of zinc nitrate (chemically pure, Beijing Chemical Plant), 29.7 grams of chromic anhydride (chemically pure, Beijing Chemical Plant), 520.9 grams of zirconium nitrate (chemically pure, Beijing Chemical Plant) Plant) was dissolved in 760 ml of deionized water, then mixed with ammonia water under stirring to form a precipitate, and the pH was controlled to 6±1, the generated precipitate was filtered, washed and dried at 200±10°C for 4 hours, and then dried at 500±60°C Calcined for 10 hours to make catalyst matrix B: Cu 0.4 ZnCr 0.3 Zr 1.95 o 5.8 .
Embodiment 3
[0028] Catalyst preparation example:
[0029] With 52.2 grams of copper nitrate (chemically pure, Beijing Chemical Plant), 13 grams of zinc nitrate (chemically pure, Beijing Chemical Plant), 28.9 grams of chromic anhydride (chemically pure, Beijing Chemical Plant), 6.9 grams of titanium dioxide (chemically pure, Beijing Chemical Plant) ) was dispersed in 280 milliliters of deionized water, and then mixed with ammonia water with a concentration of 23-25% by weight under stirring to generate a precipitate, and the pH was controlled to 7 ± 1, and the generated precipitate was filtered, washed and dried at 120°C for 6 hours, and then dried at 500 Calcined at ±60°C for 4 hours to make catalyst matrix C: Cu 5 ZnCr 6.7 Ti 2 o 20.1 .
Embodiment 4
[0031] Catalyst preparation example:
[0032] With 52.2 grams of copper nitrate (chemically pure, Beijing Chemical Plant), 20.3 grams of zinc nitrate (chemically pure, Beijing Chemical Plant), 19.6 grams of chromic anhydride (chemically pure, Beijing Chemical Plant), 4.3 grams of titanium dioxide (chemically pure, Beijing Chemical Plant) ) was dispersed in 300 milliliters of deionized water, then mixed with ammonia water with a concentration of 23-25% by weight under stirring to generate a precipitate, and the pH was controlled to 5 ± 1, and the generated precipitate was filtered, washed and dried at 120°C for 6 hours, and then dried at 500 Calcined at ±60°C for 4 hours to make catalyst precursor D: Cu 3.3 ZnCr 3 Ti 0.83 o 10.5 .
PUM
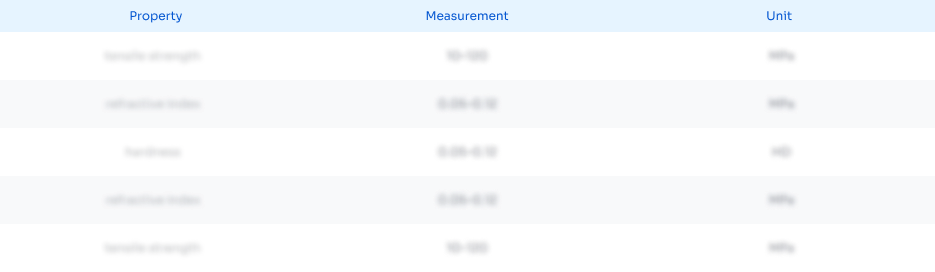
Abstract
Description
Claims
Application Information

- Generate Ideas
- Intellectual Property
- Life Sciences
- Materials
- Tech Scout
- Unparalleled Data Quality
- Higher Quality Content
- 60% Fewer Hallucinations
Browse by: Latest US Patents, China's latest patents, Technical Efficacy Thesaurus, Application Domain, Technology Topic, Popular Technical Reports.
© 2025 PatSnap. All rights reserved.Legal|Privacy policy|Modern Slavery Act Transparency Statement|Sitemap|About US| Contact US: help@patsnap.com