Wood plastic foamed material and machine-shaping process thereof
A wood-plastic foaming and processing molding technology, which is applied in the field of wood-plastic foaming materials and their processing and molding technology, can solve the problems of high material weight, light weight, high impact resistance and heat insulation, etc., and achieve high specific strength Effect
- Summary
- Abstract
- Description
- Claims
- Application Information
AI Technical Summary
Problems solved by technology
Method used
Examples
Embodiment 1
[0031] The following raw materials are used:
[0032] PE 20 copies
[0033] 65 parts wood flour
[0034] Light calcium carbonate 8 parts
[0035] Phase solvent (MHA-g-PE) 4 parts
[0036] 1 part coupling agent
[0037] Lubricant (Hst) 1 part
[0038] Foaming agent (Ac) 0.5 part
[0039] Foaming aid (ZnO) 0.5 parts
[0040] Put the wood flour into the high-speed mixer, dry it at 110-120°C, add modifiers to activate the wood flour, add additives, plastics and foaming agents and mix evenly, and discharge the material at a material temperature of 120°C Cool to 40°C in a cold mixer to form a foamable mixture.
[0041] Put the mixture into φ65 / 132 conical twin-screw extruder, heating temperature: 155°C, 165°C, 175°C, 180°C, 175°C; melt pressure 9-15Mpa; melt temperature 165-170°C ; Host speed 10-15rpm / min.
[0042] After foaming and cooling in a specially designed mold, it is shaped into wood-plastic foamed products of various shapes with continuous and evenly distributed f...
Embodiment 2
[0044] The following raw materials are used:
[0045] PP 45 parts
[0046] 45 parts wood flour
[0047] 5 parts of hollow glass microspheres
[0048] Phase solvent (MHA-g-PE) 1.5 parts
[0049] 0.5 parts of coupling agent
[0050] Lubricant (Hst) 0.2 parts
[0051] Antioxidant 0.5 parts
[0052] 0.2 parts of cross-linking agent
[0053] Auxiliary cross-linking agent 1 part
[0054] Foaming agent (Ac) 0.6 part
[0055] Foaming aid (ZnO) 0.5 parts
[0056] Put the wood flour into the high-speed mixer, dry it at 110-120°C, add modifiers to activate the wood flour, add additives, plastics and foaming agents and mix evenly, and discharge the material at a material temperature of 120°C Cool to 40°C in a cold mixer to form a foamable material.
[0057] The foamable material is put into a φ65 single-screw extruder, the processing temperature is: 175°C, 195°C, 210°C, 195°C; the screw speed is 40rpm / min.
[0058] After foam molding in a hot compression molding machine, it is ...
Embodiment 3
[0060] The following raw materials are used:
[0061] PE 65 parts
[0062] 25 parts wood flour
[0063] Precipitated barium sulfate 4 parts
[0064] Phase solvent 2.5 parts
[0065] 0.5 parts of coupling agent
[0066] Lubricant 1 part
[0067] Foaming agent (Ac) 1.5 parts
[0068] Foaming aid (ZnO) 0.5 part
[0069] Put the wood flour into the high-speed mixer, dry it at 110-120°C, add modifiers to activate the wood flour, add additives, plastics and foaming agents and mix evenly, and discharge the material at a material temperature of 120°C Cool to 40°C in a cold mixer to form a foamable material.
[0070] The foamable material was put into a φ65 single-screw extruder, the processing temperatures were: 160°C, 170°C, 185°C, 170°C; the screw speed was 35rpm / min.
[0071]After foam molding in a hot compression molding machine, it is formed into a wood-plastic foam product with continuous and evenly distributed foam micropores, and the density is 0.45-0.6.
PUM
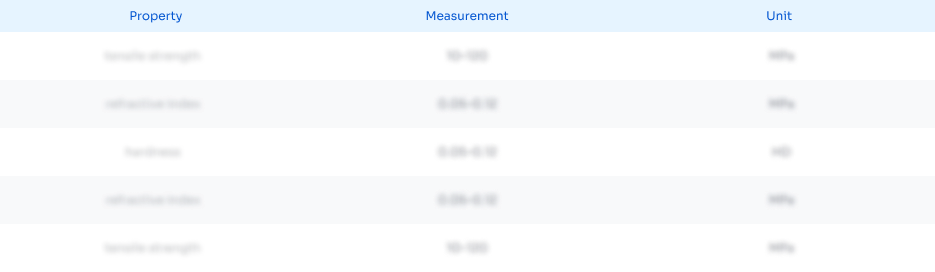
Abstract
Description
Claims
Application Information

- R&D Engineer
- R&D Manager
- IP Professional
- Industry Leading Data Capabilities
- Powerful AI technology
- Patent DNA Extraction
Browse by: Latest US Patents, China's latest patents, Technical Efficacy Thesaurus, Application Domain, Technology Topic, Popular Technical Reports.
© 2024 PatSnap. All rights reserved.Legal|Privacy policy|Modern Slavery Act Transparency Statement|Sitemap|About US| Contact US: help@patsnap.com