Method for processing hidh-precision sub-photoetched pattern on substrate
A sub-lithography, high-density technology, applied in the field of processing high-density sub-lithography patterns, can solve problems such as density increase
- Summary
- Abstract
- Description
- Claims
- Application Information
AI Technical Summary
Problems solved by technology
Method used
Image
Examples
Embodiment Construction
[0030] In the following detailed description and some of the drawings, similar elements are identified with similar reference numerals.
[0031] As shown in the illustrative figures, the present invention is embodied in a method of fabricating high density sublithographic patterns. The method involves depositing a masking layer on a substrate and then patterning the masking layer to form an image comprising a feature size that is larger than the photolithography used to pattern the masking layer. The minimum resolution of the system is greater or equal. The masking layer is then etched to transfer the image onto the substrate, thereby defining features on the substrate. This graph includes the minimum feature size, as well as horizontal and vertical sidewall surfaces.
[0032] Spacer material is deposited over the features to cover the horizontal surfaces and vertical sidewall surfaces. The deposition process continues until the spacer material has a predetermined thickness...
PUM
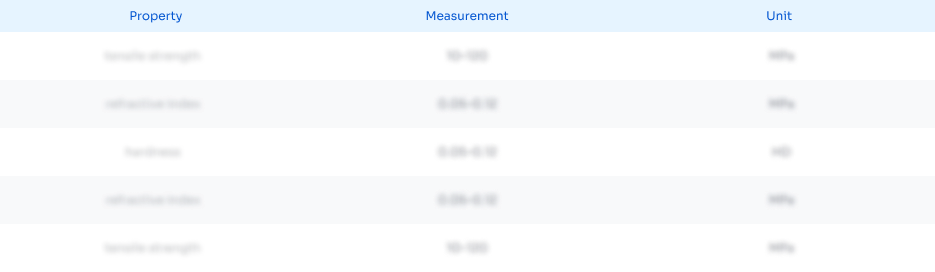
Abstract
Description
Claims
Application Information

- R&D Engineer
- R&D Manager
- IP Professional
- Industry Leading Data Capabilities
- Powerful AI technology
- Patent DNA Extraction
Browse by: Latest US Patents, China's latest patents, Technical Efficacy Thesaurus, Application Domain, Technology Topic, Popular Technical Reports.
© 2024 PatSnap. All rights reserved.Legal|Privacy policy|Modern Slavery Act Transparency Statement|Sitemap|About US| Contact US: help@patsnap.com