Converter retaining operation method of preventing splash slag and reducing iron loss
A technology for protecting furnaces and converters by slag splashing, which is applied in the manufacture of converters, etc., and can solve problems such as difficulty in settling iron beads in slag, increased iron loss in slag, and affecting the effect of slag splashing on furnace protection, etc.
- Summary
- Abstract
- Description
- Claims
- Application Information
AI Technical Summary
Problems solved by technology
Method used
Image
Examples
Embodiment
[0017] Example: 50-ton converter, the furnace campaign is in the middle stage. After the converter stops blowing, the steel will not be tapped immediately. Instead, powdered graphite and light-burned dolomite (1.2 kg of carbon / ton steel are added at a time) are added to the furnace first, and the steel will be tapped after the reaction is completed. Steel, because the furnace body is in the tapping position, the slag spreading surface area is large, the slag layer is thin, and the graphite powder is evenly blown, so that the area of the TFe boundary between the graphite powder and the slag is greatly increased. At the same time, the amount of graphite powder blown in is small (ton steel 1.2 kg), so that the temperature drop of the slag is small. At this time, the viscosity of the slag is small, the (FeO) diffusion rate is fast, and the generated CO bubbles are easy to overflow. Therefore, the reaction between C-(FeO) is relatively sufficient, so that the FeO in the slag is great...
PUM
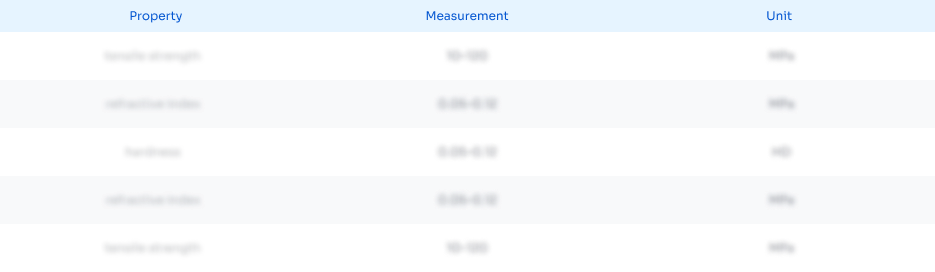
Abstract
Description
Claims
Application Information

- Generate Ideas
- Intellectual Property
- Life Sciences
- Materials
- Tech Scout
- Unparalleled Data Quality
- Higher Quality Content
- 60% Fewer Hallucinations
Browse by: Latest US Patents, China's latest patents, Technical Efficacy Thesaurus, Application Domain, Technology Topic, Popular Technical Reports.
© 2025 PatSnap. All rights reserved.Legal|Privacy policy|Modern Slavery Act Transparency Statement|Sitemap|About US| Contact US: help@patsnap.com