Epoxidation process using serially connected cascade of fixed bed reactors
A fixed bed reactor, epoxidation technology, applied in chemical instruments and methods, organic chemistry, chemical recovery, etc., can solve problems such as expensive catalysts
- Summary
- Abstract
- Description
- Claims
- Application Information
AI Technical Summary
Problems solved by technology
Method used
Image
Examples
Embodiment comparative example 1
[0035] A conventional multi-bed reaction vessel (1) is used, where as figure 1 As shown, five reactor beds (A, B, C, D, E) are stacked. Containers of this general type are described in more detail, for example, in U.S. Patent Nos. 2,271,646 and 2,322,366. The reactor bed was simultaneously loaded with a total of 65 Kg of a titania-coated silica heterogeneous catalyst freshly prepared as described in U.S. Patent No. 3,829,392. A feed comprising 286 Kg / hr of ethylbenzene oxide and 408 Kg / hr of propylene was introduced via line 2 to the bottom bed of the reaction vessel, maintained in the liquid phase by operating at a pressure of 800 psia. Oxidized ethylbenzene is obtained by conventional molecular oxygen oxidation of ethylbenzene as described in U.S. Patent No. 4,066,706, containing about 35% by weight ethylbenzene hydroperoxide.
[0036] At the beginning of the epoxidation cycle, the temperature of the feedstock was about 38°C, initially bypassing the heat exchanger attached...
Embodiment 2
[0045] According to the present invention, if figure 2 A row of 6 individual reaction vessels (A, B, C, D, E, F) is shown arranged. Only 5 reaction vessels are serially connected by lines and used in the conversion operation at any given time. figure 2shows the row of reactors in a given epoxidation cycle in which the feed stream is sent first through reactor A, then reactor B, then reactor C, then reactor D, and finally through reactor E, so that reactor F is not in operation. Each reaction vessel contained a fixed bed comprising 13 Kg of silica catalyst on top of titania. Each reaction vessel was separated by a valve to allow one vessel to be closed at a time for catalyst bed replacement. The feed composition and feed rate were the same as those used in Comparative Example 1. Using heat exchangers (HE-1, HE-2, HE-3, HE-4), the inlet temperature of the feed stream introduced into each catalyst bed was controlled so that the outlet temperature did not exceed 121°C. That...
Embodiment 3
[0053] In this example, the epoxidation process was performed in the same manner as described in Example 2, except that at the end of the epoxidation cycle, the first reaction vessel in the sequence (reactor A) was removed from operation and replaced with The idle reaction vessel (Reactor F) was replaced by fresh catalyst. As a result, the feed stream is introduced first into the reaction vessel series containing the most active catalyst rather than, as in Example 2, the reaction vessel containing the least active catalyst. In the next epoxidation cycle, the reactor sequence is thus F-B-C-D-E. In subsequent cycles, the reactor containing the least active catalyst is again removed from operation and the feedstream is passed first through the replacement reactor with the most active catalyst in the series, and thereafter through the remaining operating reactors in order of increasing catalyst activity. reactor. In the third cycle, the reactor sequence will be eg A-C-D-E-F, wit...
PUM
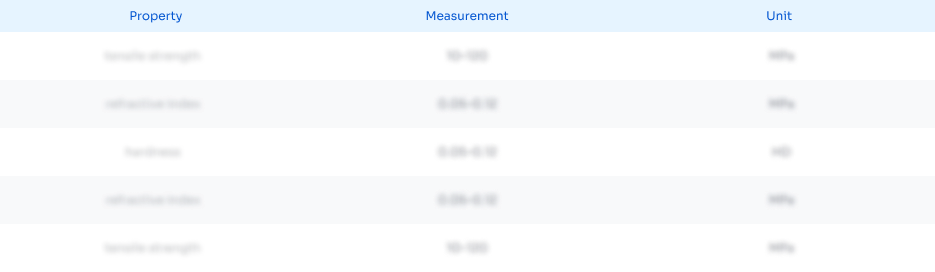
Abstract
Description
Claims
Application Information

- R&D
- Intellectual Property
- Life Sciences
- Materials
- Tech Scout
- Unparalleled Data Quality
- Higher Quality Content
- 60% Fewer Hallucinations
Browse by: Latest US Patents, China's latest patents, Technical Efficacy Thesaurus, Application Domain, Technology Topic, Popular Technical Reports.
© 2025 PatSnap. All rights reserved.Legal|Privacy policy|Modern Slavery Act Transparency Statement|Sitemap|About US| Contact US: help@patsnap.com