Method for preparing resin type water-retaining preparation
A water-retaining agent and resin-based technology, which is applied in the field of preparation of resin-type water-retaining agents, can solve the problems of reduced distilled water absorption capacity, complex process, and low salt water absorption rate, and achieve fast water absorption rate, wide application range, and low reaction temperature. Effect
- Summary
- Abstract
- Description
- Claims
- Application Information
AI Technical Summary
Problems solved by technology
Method used
Examples
Embodiment 1
[0019] Starch, acrylic acid and acrylamide are used as raw materials, the redox system formed by potassium persulfate-sodium bisulfite is used as the initiator, and N, N'-methylenebisacrylamide is used as the cross-linking agent for ternary copolymerization. Proceed as follows:
[0020] The mass ratio of starch to acrylic acid and acrylamide is 1:0.4:0.08. First, mix 2g of starch and 30g of distilled water evenly, then gelatinize in a reactor at a gelatinization temperature of 75°C; then use potassium hydroxide to neutralize acrylic acid and alkali The degree of melting is 80%. After cooling to room temperature, pour it into the reactor together with the acrylamide aqueous solution and mix with the gelatinized starch; then add 4.0×10 -3 mol L -1 Initiator, 0.08mol L -1 The cross-linking agent and the initiator are redox systems formed by potassium persulfate and sodium bisulfite at a mass ratio of 1:0.8, and the addition method of potassium persulfate and sodium bisulfite is...
Embodiment 2
[0022] The difference from Example 1 is:
[0023] The mass ratio of starch to acrylic acid and acrylamide is 1:0.2:0.03. First, mix 5g of starch and 20g of distilled water evenly, then gelatinize in the reactor, and the gelatinization temperature is 70°C; then use potassium hydroxide to neutralize acrylic acid, alkali The melting degree is 90%. After cooling to room temperature, pour it into the reactor together with the acrylamide aqueous solution and mix with the gelatinized starch; then add 1.5×10 -3 mol L -1 Initiator, 0.04mol L -1 The cross-linking agent and the initiator are redox systems formed by potassium persulfate and sodium bisulfite at a mass ratio of 1:0.1, and the addition method of potassium persulfate and sodium bisulfite is sequentially added. in N 2 Under protection, the polymerization reaction temperature is 25°C and stirred for 1.5 hours until the end of the polymerization reaction; the pH is adjusted to neutral with lye; the grafted product is washed a...
Embodiment 3
[0025] The difference from Example 1 is:
[0026] The mass ratio of starch to acrylic acid and acrylamide is 1:0.5:0.02. First, mix 4g of starch and 40g of distilled water evenly, then gelatinize in a reactor at a gelatinization temperature of 90°C; then use potassium hydroxide to neutralize acrylic acid and alkali The degree of melting is 60%. After cooling to room temperature, pour it into the reactor together with the acrylamide aqueous solution and mix with the gelatinized starch; then add 6.0×10 -3 mol L -1 Initiator, 0.1mol L -1 The cross-linking agent and the initiator are redox systems formed by potassium persulfate and sodium bisulfite at a mass ratio of 1:0.3, and the potassium persulfate and sodium bisulfite are added in sequence. in N 2 Under protection, the polymerization reaction temperature is 30°C and stirred for 1 hour until the end of the polymerization reaction; the pH is adjusted to neutral with lye; the grafted product is washed and filtered and then dr...
PUM
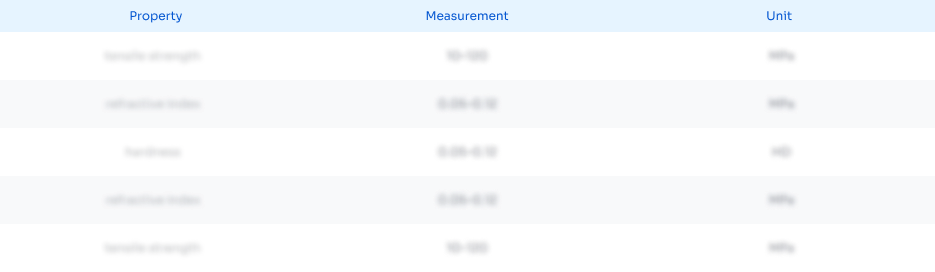
Abstract
Description
Claims
Application Information

- R&D
- Intellectual Property
- Life Sciences
- Materials
- Tech Scout
- Unparalleled Data Quality
- Higher Quality Content
- 60% Fewer Hallucinations
Browse by: Latest US Patents, China's latest patents, Technical Efficacy Thesaurus, Application Domain, Technology Topic, Popular Technical Reports.
© 2025 PatSnap. All rights reserved.Legal|Privacy policy|Modern Slavery Act Transparency Statement|Sitemap|About US| Contact US: help@patsnap.com