Silver alloy etching solution
A technology of silver alloy and etching solution, applied in the field of etching solution, can solve the problems of not having, not widely used in wafer or panel yellow light manufacturing process, low resistance, etc., and achieving the effect of novel composition
- Summary
- Abstract
- Description
- Claims
- Application Information
AI Technical Summary
Problems solved by technology
Method used
Examples
Embodiment 1-8
[0053] Mix hydrogen peroxide and nitric acid in the ratio of Table 1 below, and add water to 100 grams to prepare the etching solution with the following concentration. A silicon substrate with a silver alloy thin film is spin-coated, and a photoresist layer is coated on it; wherein the silver alloy thin film is formed on the silicon substrate by a sputtering method, and contains more than 98% silver, 0.9% Palladium and 1.0% copper. Subsequently, the silicon substrate was exposed to light to form a patterned photoresist layer; the silicon substrate was then coated or immersed in the etching solution configured according to Table 1, and the etching rate was measured. The results are shown in Table 1 below.
[0054] Example
[0055] After the etching was completed, the silicon substrate was inspected and the photoresist of the silicon substrate and the pattern was not damaged. Therefore, the etching solution only selectively etches the silver alloy.
Embodiment 9-23
[0057] Mix hydrogen peroxide and sulfuric acid in the ratio of Table 2 below, and add water to 100 grams to prepare the etching solution with the following concentration. A photoresist layer is coated on a silicon substrate with a silver alloy thin film by spin coating; wherein the silver alloy thin film is formed on the silicon substrate by a sputtering method, and contains more than 98% silver, 0.9 % Palladium and 1.0% copper. Subsequently, the silicon substrate was exposed to light to form a patterned photoresist layer; the silicon substrate was then coated or immersed in the etching solution configured according to Table 2, and the etching rate was measured. The results are shown in Table 2 below.
[0058] Example
[0059] After the etching was completed, the silicon substrate was inspected and the photoresist of the silicon substrate and the pattern was not damaged. Therefore, the etching solution only selectively etches the silver alloy.
Embodiment 24-32
[0061] Mix the solution with hydrogen peroxide, sulfuric acid, and ammonium acetate according to the ratio of Table 3 below, and add water to 100 grams to prepare the etching solution with the following concentration. A silicon substrate with a silver alloy thin film is spin-coated, and a photoresist layer is applied to it; wherein the silver alloy thin film is formed on the silicon substrate by a sputtering method, and contains more than 98% silver, 0.9% Palladium and 1.0% copper. Subsequently, the silicon substrate was exposed to light to form a patterned photoresist layer; the silicon substrate was then coated or immersed in the etching solution configured according to Table 3, and the etching rate was measured. The results are shown in Table 3 below.
[0062] Example
[0063] After the etching was completed, the silicon substrate was inspected and the photoresist of the silicon substrate and the pattern was not damaged. Therefore, the etching solution only selectiv...
PUM
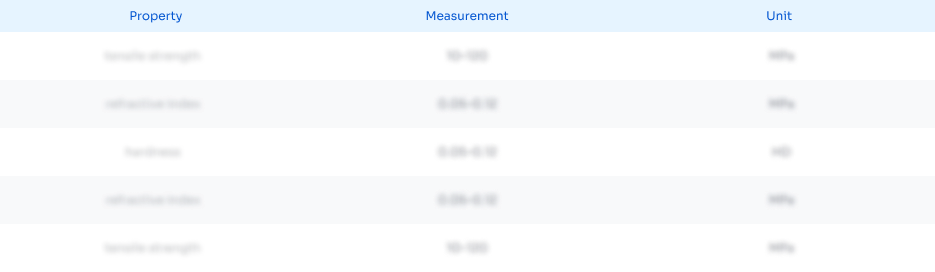
Abstract
Description
Claims
Application Information

- Generate Ideas
- Intellectual Property
- Life Sciences
- Materials
- Tech Scout
- Unparalleled Data Quality
- Higher Quality Content
- 60% Fewer Hallucinations
Browse by: Latest US Patents, China's latest patents, Technical Efficacy Thesaurus, Application Domain, Technology Topic, Popular Technical Reports.
© 2025 PatSnap. All rights reserved.Legal|Privacy policy|Modern Slavery Act Transparency Statement|Sitemap|About US| Contact US: help@patsnap.com